Insights
KR Decarbonization Magazine
VOL.04 | Autumn 2023
IMO DCS 기반 CII 등급 분석 및 개선방안
![]() KR 친환경기술팀 김동기 선임 |
현존선의 CII등급 향상을 위해서는
|
2023년부터 국제 항해에 종사하는 5,000GT 이상의 선박(MARPOL 부속서 6의 26.3 규칙 적용 대상 선박)을 대상으로 CII 규제가 도입되었다. 이에 따라 선사들은 현재 자사 선박의 CII등급 예상 결과에 촉각을 곤두세우고 있다.
이러한 상황 속에서 KR은 선사에 사전 CII등급 현황 정보를 제공하고자 IMO DCS 데이터를 기반으로 CII등급 사전 분석을 진행하였다. 분석 과정에 사용한 IMO DCS 데이터의 경우, 2023년 데이터가 현재 모니터링 중인 상황을 감안하여 2022년도 데이터를 사용하였다.
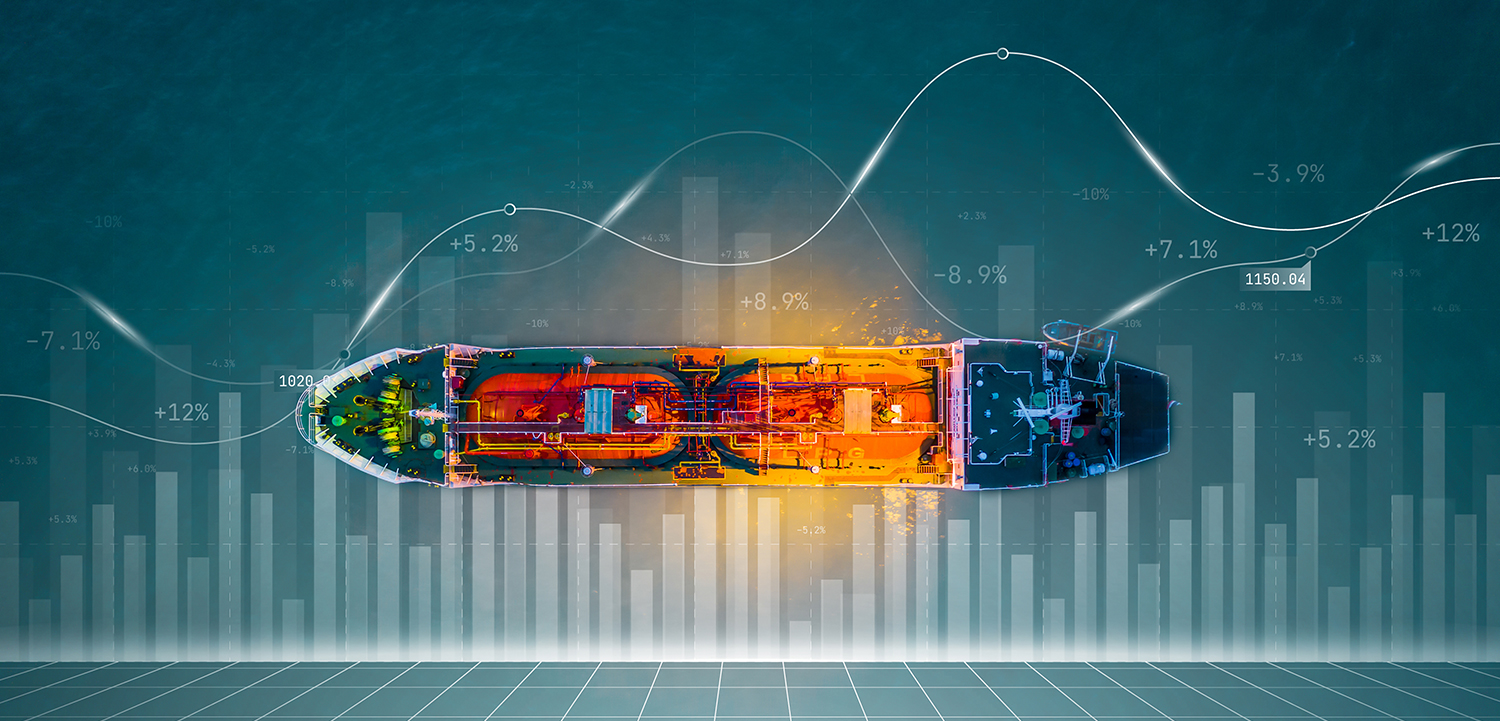
2022년도 IMO DCS 데이터 기반의 CII등급 분석
진행 결과, 2023년에는 약 2,000여 척의 2022년도 IMO DCS 데이터가 KR GEARs를 통해 제출 및 검증이 완료되었으며, 해당 선박들을 대상으로 한 사전 CII등급 분석 결과는 다음의 그래프를 통해 확인할 수 있다.
2022년도 CII등급 사전 분석 결과
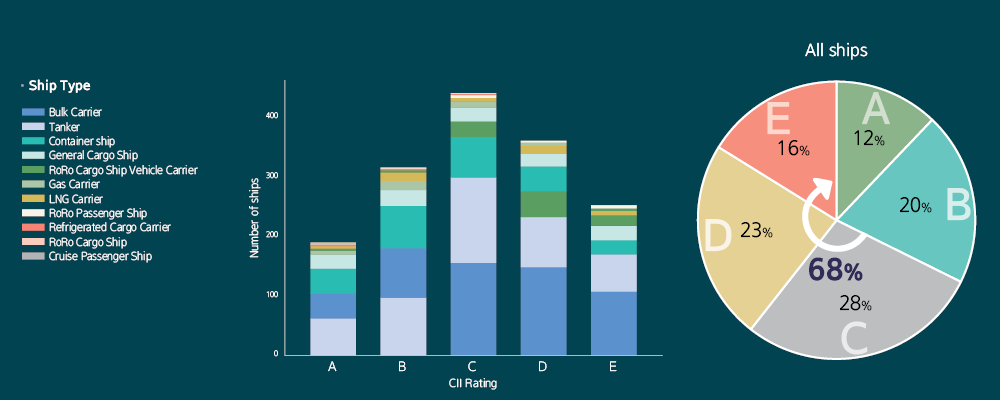
먼저, 선종별 CII등급 분포 현황을 척수와 비율을 기준으로 분석하였다. 전 선박의 CII등급 비율을 분석한 결과, E등급을 부여받은 선박은 16%, D등급을 부여받은 선박은 23%, C등급을 부여받은 선박은 약 28%인 것으로 분석되었다. 이를 통해서, C에서 E등급까지 부여받은 선박의 비율은 총 68%나 되는 것이 확인되었다. C등급 선박의 경우에도 매년 CII 허용값이 강화되어 향후에 D혹은 E등급을 부여받을 가능성이 있다는 점을 고려한다면, D등급 및 E등급 선박뿐만 아니라 C등급 선박 역시 CII등급 향상을 위한 적절한 조치방안을 검토하고 수행해야 한다는 것을 알 수 있다.
다음의 원 그래프는 KR에 제출된 선종 중 4개 선종(벌크선, 탱커, 컨테이너선, LNG운반선)의 CII등급 비율을 나타내고 있다.
선종별 CII등급 비율
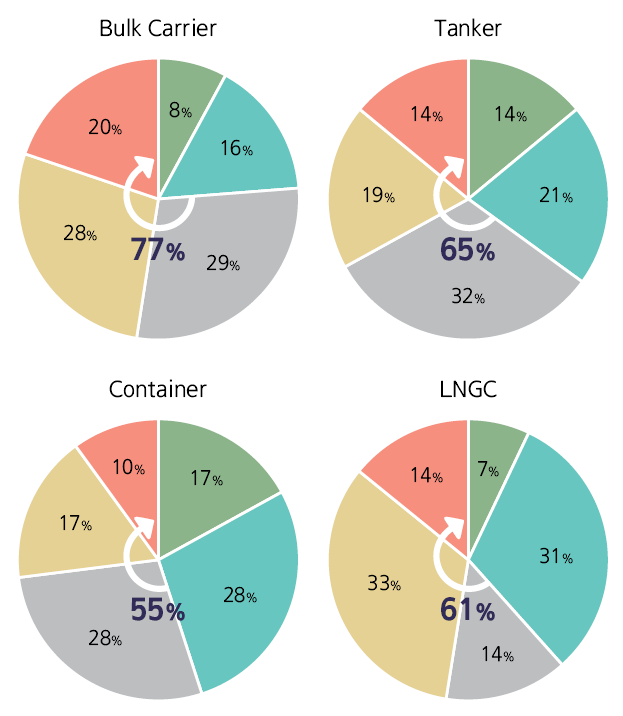
벌크선의 경우, C~E등급의 선박의 비율이 77%로 전체 선박의 CII등급 비율 및 타 선종 대비 높은 것으로 분석되었으며, 상대적으로 컨테이너선은 C~E등급 선박의 비율이 55%로 전체 평균치인 69%보다 낮은 것으로 분석되었다.
이는 주로 정기선으로 구성되어 체선 시간이 짧은 컨테이너선과 달리, 벌크 및 탱커선대는 부정기선의 비율이 높아 체선 시간이 상대적으로 길어 하위 CII등급의 비율이 더 높은 것으로 판단된다. LNGC의 경우에도 열 효율이 낮은 스팀 터빈을 추진기관으로 사용하는 선박이 다수 존재하여 C~E등급의 선박이 61%나 되는 것으로 분석되었다.
또한, 운항 거리 및 DWT를 기반으로 CII등급을 분석한 결과, 다음 그래프와 같이 일반적으로 운항 거리가 짧은 선박들은 하위 등급인 C~E등급의 비율이 높으며, 상대적으로 DWT가 큰 선박 대비 DWT가 작은 선박들의 C~E등급 비율이 높은 것으로 분석되었다. 추가적으로, 선박 DWT가 상대적으로 작으면서 단거리 항차의 비율이 높은 선박의 경우에는 E등급 비율이 높으며, DWT가 크면서 장거리 항차의 비율이 높은 선박은 상위 등급의 비율이 높은 것을 확인하였다.
운항 거리 및 DWT CII등급
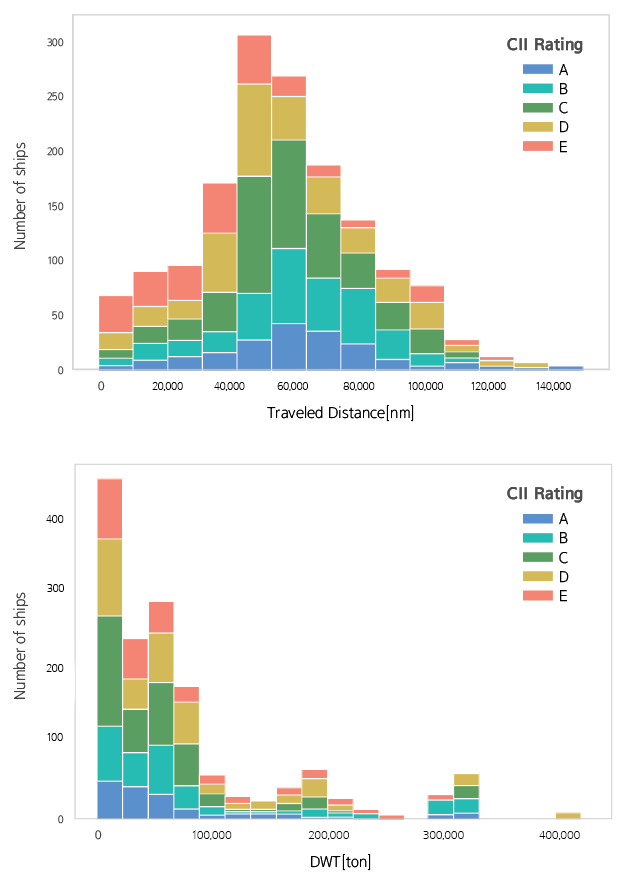
IMO에서도 선종, 운항 거리, 항만 대기 시간 등에 따른 CII 측면에서의 불이익이 존재한다는 것을 인지하고 있어, 단기 조치 검토 과정에서 CII 보정계수 및 항차 조정 사항(단거리 항차 및 항만 대기 시간, Ship-to-Ship 화물 운송 작업에 종사하는 자가 하역 벌크선, 스팀 터빈 추진 LNGC, 가스 운반선 보일러 연료 소모량 및 불활성 가스 발생기 사용에 대한 보정계수 등)을 검토할 예정이다.
선박의 CII등급 변화와 개선조치 필요성
앞서 전체 선박 및 선종별 관련 데이터를 살펴보았다면, 이제 개별 선박에 대한 데이터 분석 결과를 살펴보고자 한다. 전체 선박 중 핸디 사이즈 벌크선 1척을 선정하였으며, 해당 선박은 2022년도를 기준으로 B등급을 획득하였다. 'MEPC 80차 회의에서 유지된 2008년 대비 2030년까지 탄소집약도 40% 감축 목표'를 기반으로 2027~2030년 사이에 매해 탄소집약도가 2.75%씩 감소한다 가정하고, 2023년부터의 CII 예상 등급을 다음 그래프와 같이 분석하였다. 그래프 중, 왼쪽의 그래프는 CII등급 개선조치를 취하지 않을 경우 2030년도까지의 등급 변화를 나타낸다. 오른쪽 그래프는 최소 C등급을 유지하기 위한 온실가스 감축 필요량을 비율로 나타내고 있다.
2023~2026년까지 해당 선박의 CII등급은 C등급이며, 2027년에는 D등급, 2028년부터는 D에서 E등급으로 변화할 것으로 예상되며, 늦어도 2027년부터는 최소 C등급을 유지하기 위해 개선 조치가 시행되어야 하는 것으로 분석되었다.
CII등급 개선조치 미시행 시 등급 변화
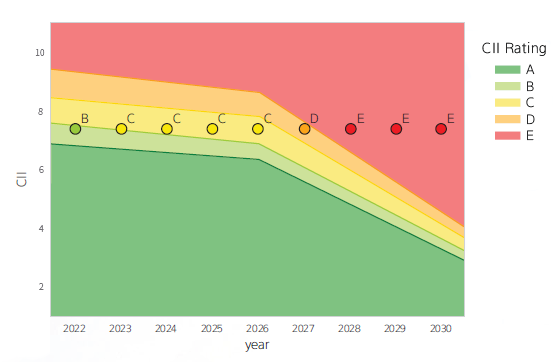
C등급 유지를 위한 온실가스 감축 필요량
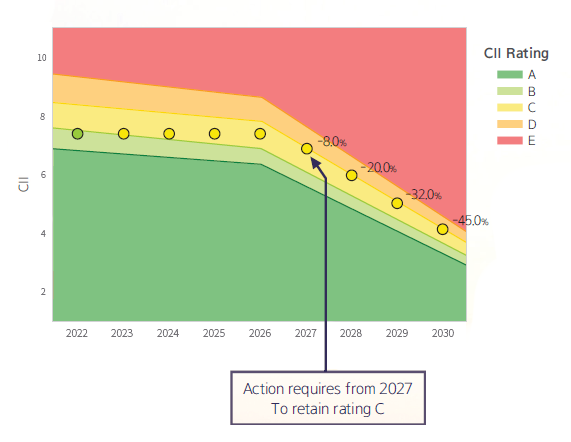
현존선의 CII등급의 향상을 위한 조치 방안
그렇다면, 선사는 현존선의 CII등급 향상을 위해서 어떠한 조치를 취할 수 있을까?
CII등급을 향상시키기 위한 조치 중 첫 번째로, 선속 감소를 들 수 있다. 그러나 영업 및 선박 운항 측면에서 낮출 수 있는 최저 선속까지 낮추고도 추가적인 온실가스 감축이 요구되는 경우에는 Weather Routing을 통한 선속 및 항로 최적화 기술, 정시 도착, 최적 트림 유지, 주기적인 프로펠러 및 선체 소제, 육상 전력 사용 등 다른 조치와 병행하여 시행해야 한다.
두 번째, 연료의 전환을 고려할 수 있다. 현 시점에서 실현 가능한 가장 우선적인 대안은 바이오 연료를 사용하는 것이다. 최근 IMO는 MEPO 80차 회의에서 MARPOL Annex VI의 26, 27 및 28규칙(DCS 및 CII) 측면의 바이오 연료 사용에 관한 잠정 지침을 MEPC.1/Circ.905으로 승인하였다. 본 가이드라인에서 제시하는 요건을 만족하는 바이오 연료를 사용하면 온실가스 감축 효과를 얻을 수 있을 것으로 예상된다. 다만, 연료 공급에 대한 불안정성이 존재하여 충분한 연료를 공급받기 위한 연료 수급처 확보가 필요하며, 기존 연료 대비 비싼 가격을 고려하여야 한다.
세 번째, 선박의 저항을 감소시키거나 추진 효율을 향상시킬 수 있는 기술을 선박에 적용하여 에너지 효율을 개선하는 것이다. 가장 쉽게는 저마찰 도료 적용부터 낮아진 선속에 맞는 프로펠러로의 교체, 에너지 효율 개선 장치(ESD)의 설치를 고려해볼 수 있다. 그러나 에너지 효율 개선 장치의 온실가스 감축 효과에 대한 불확실성과 CAPEX 및 OPEX를 고려한 신중한 접근이 필요하다.
앞서 소개한 조치는 가장 대표적인 조치를 서술한 것이며, 언급된 조치 중 하나만 적용하는 것이 아니라 적용 가능한 조치들을 모두 검토한 뒤 선박별로 적절한 조합을 선정하는 것이 바람직하다. 예를 들어, 선속 감소와 Weather Routing을 통한 항로 최적화 기술을 적용한 뒤, 일정 부분 바이오 연료를 사용할 수 있다. 바이오 연료의 경우에도, 온실가스 감축 필요량에 따라 블렌딩 비율이 다른 바이오 연료를 수급 받아 사용할 수도 있다.
효과적인 탈탄소화 대응을 위한 규제 대응 디지털화
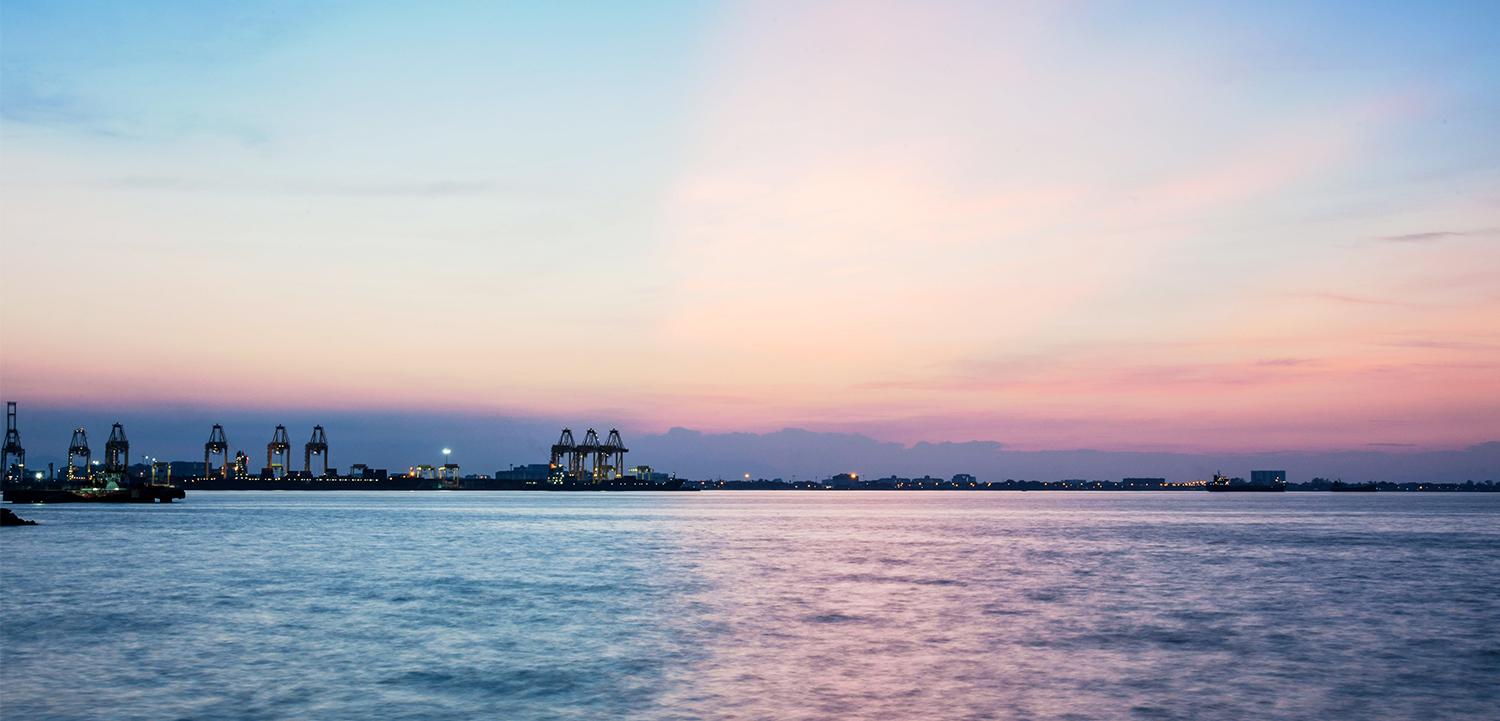
현재, CII 규제의 목표치인 C등급 미달성시 선박에게 주어지는 패널티로는 시정 조치 계획이 담긴 SEEMP Part III 제출 및 재승인만 있을 뿐, 출항 정지 등과 같은 명확한 가이드라인이 없어 선사가 적극적으로 대응하지 않는 경우도 확인되고 있다. 그러나 2026년 1월 1일까지 완료되어야 하는 단기 조치의 효과성 검토 결과에 따라서, 시정 조치 선박을 대상으로 출항 정지와 같은 패널티를 강화하는 방안 등이 논의될 수 있으므로 사전에 온실가스 감축에 대한 선사의 노력이 절실히 요구된다.
KR에서는 선사의 온실가스 규제 대응 지원을 위해 KR GEARs를 통한 CII, EU/UK MRV, ETS 규제까지 대응 가능한 원스톱 토탈 솔루션을 제공하고 있다. 선사는 실시간 운항 데이터를 기반으로 CII등급을 도출하고 관리할 수 있는 CII 모니터 기능과 선박별 개선 시나리오 수립을 통한 CII 시뮬레이터 기능을 통해 CII 규제에 대응할 수 있다.
이에 추가하여, KR은 매년 검증 완료된 DCS 데이터를 기반으로 하여 대상 선박의 CII 현황, 타 선사 선박과의 CII 현황 비교, 2030년까지의 CII 예상 등급 및 상위 등급 획득을 위한 온실가스 감축 필요량 비율 산정 등의 내용을 담은 GHG Countermeasure Advisory Report를 제공할 계획이며, 해당 Report는 각 선사에 배포될 예정이다. 해당 정보는 CII 규제 대응과 관련한 향후 계획 및 의사 결정에 있어 유용한 자료로 활용될 것으로 예상된다.
KR은 가속화되는 해운의 탈탄소화 대응을 위해 에너지 절감 및 온실가스 배출 감축 기술 개발뿐만 아니라 행정 비용 절감, 업무 효율성 증대 등을 위하여 규제 대응에 있어서의 디지털화가 필수적이라고 판단하고 있다.
규제 대응 디지털화는 양질의 데이터 수집 및 관리와 운항 데이터의 실시간 모니터링을 통해 선제적인 CII 규제 대응 및 탈탄소화 전략 수립을 가능하게 할 것이다.
KR은 선사의 규제 대응 디지털화 및 해운 탈탄소화 지원을 위하여 KR GEARs 기능을 지속적으로 업데이트하고, GHG Countermeasure Advisory Report를 제공하는 등 노력을 기울여 나갈 예정이다.
선박 대체 연료와 연료 저장 장치 기술 이야기
![]() KR 기술영업지원팀 심영진 책임 |
연료 저장 장치 기술은 선박의
|
선박 대체 연료 전망과 연료 선택
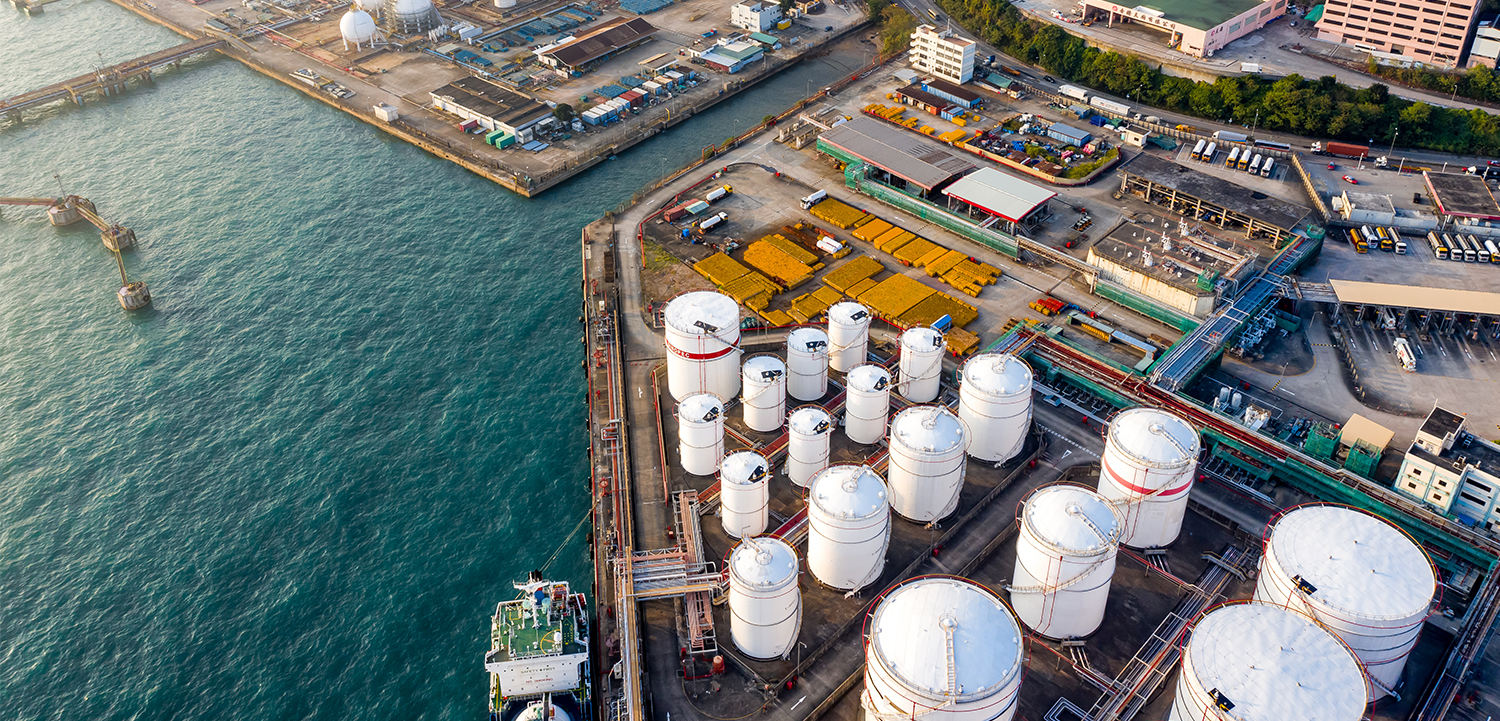
지금까지는 화석 연료를 기반으로 한 한 가지 선박 연료가 독점적으로 사용되었던 시대였다. 하지만 2000년대 중반부터 각 연료의 고유한 장단점과 기술 및 상업적 성숙도의 차이 그리고 선박 종류별 특수성 등을 이유로 점차 다양한 연료를 사용하는 시대로 전환되고 있다.
현재 논의되는 미래의 대체 연료는 LNG, LPG, 메탄올, 암모니아, 에탄, 수소, 배터리, 소형 원자로 등 매우 다양하다. 지난 10년 동안 주목받았던 대체 연료 중에 LNG 연료의 사용 비중이 증가하고 있으며, 메탄올 연료 사용도 점차 늘어나고 있다. 그러나 메탄올은 주로 특정 선종인 컨테이너선 등의 연료로 선택되고 있다. 한편 암모니아, 수소, 소형 원자로 연료는 기술적 문제와 독성 문제 등으로 인해 아직 선박용 연료로 적용되고 있지는 않다.
특히 선박 연료로서 각 연료들을 사용하기 위해서는 주요한 단계인 엔진 개발이 필수적이다. 암모니아의 경우, 2024~2026년경 주엔진의 개발이 완료되고 나면 점차 암모니아 추진 선박 발주가 늘어날 것으로 예상된다. 그 이후 수소, 소형 원자로 기술 등으로 연료 선택이 바귀어 갈 것으로 예상된다.
‘연료 선택’은 연료 가격, 설비 비용, 탈탄소 규제 비용, 개조 비용 등 다양한 요소를 고려해야 하는 복잡한 결정이다. 이런 미래의 불확실성으로 인해 각 해운사는 자신의 상황에 맞는 전략 수립을 하는 것이 필요하다. 다양한 가능성 때문에 연료 다양성, 연료 모자이크, 연료 유연성과 같은 개념이 중요해지고 있으며, 이런 상황 속에서 대체 연료 엔진 기술과 더불어 연료 저장 장치(Fuel Containment System) 기술이 선박의 배치, 건조 가격, 선박 운항에 미치는 영향은 매우 높다. 따라서 지금부터 연료 저장 장치 기술을 해운산업 탈탄소화 관점에서 살펴보도록 하겠다.
전체 선대 연료 선택 현황
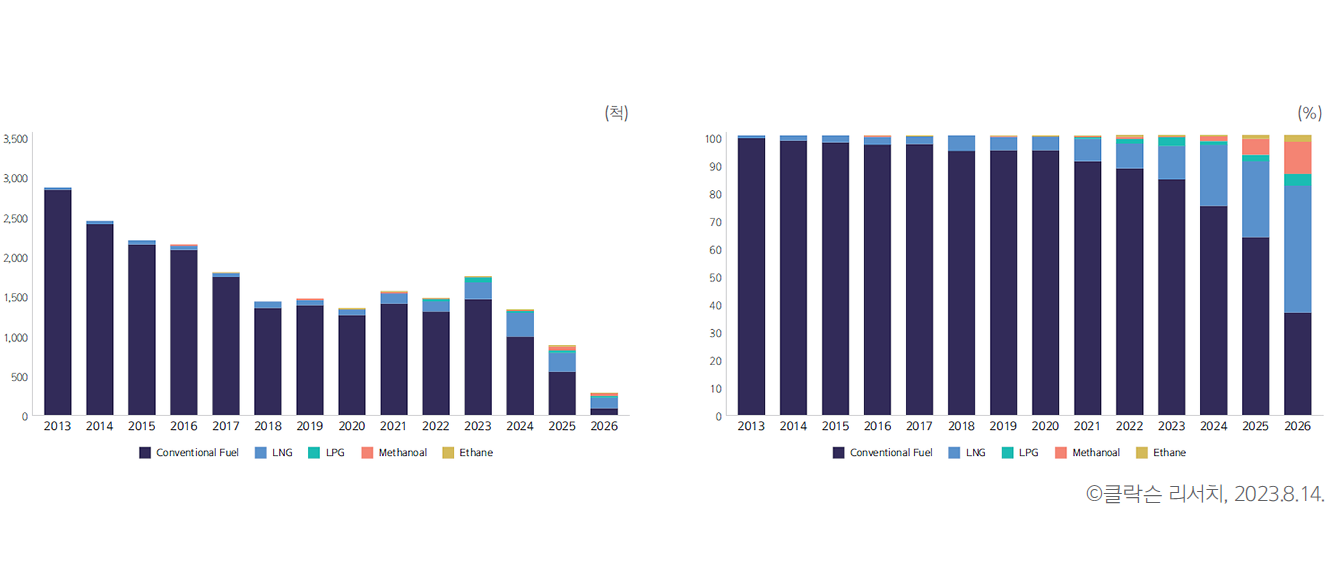
선종별 연료 발주 현황
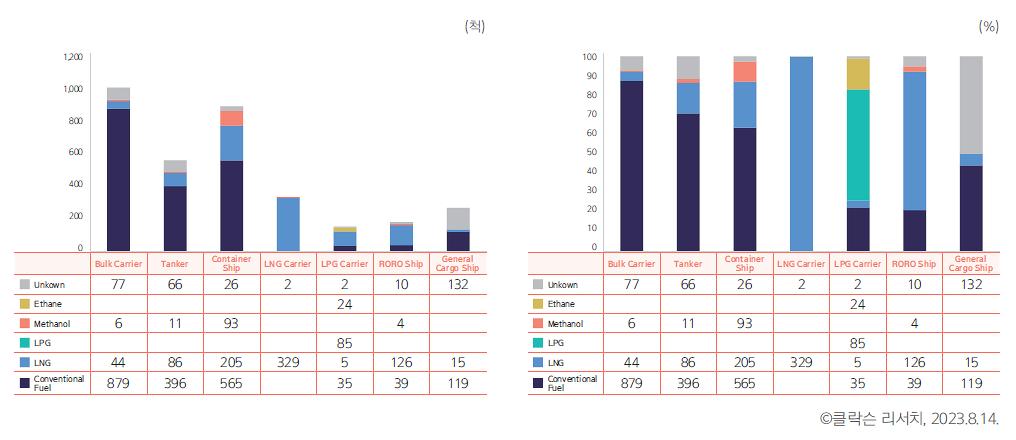
미래 대체 연료 저장 장치 기술의 종류와 재료
· 대체 연료 저장 장치 기술의 선택
다양한 대체 연료의 선택 가능성은 선박 설계를 어렵게 한다. 동일 선종이라도 다양한 대체연료 중에 어떤 대체 연료를 선택하는지에 따라 연료 탱크의 형태의 형식, 배치, 재료 등이 달라지며 그것들은 선박 전체에 영향을 미치기 때문이다.
성공적인 대체 연료 저장 장치의 설계를 위하여 다음과 같은 흐름도를 작성해 보았다.
대체 연료 저장 탱크 설계 흐름도
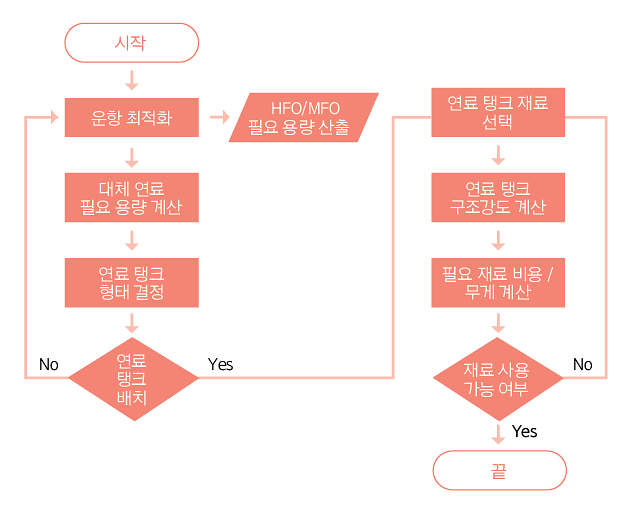
우선적으로 결정하여야 하는 것은 선박의 운항 최적화이다. 어떤 항로를 얼마만큼 운항하는지에 따라 필요 연료의 양이 결정되기 때문이다. 운항에 필요한 기존 연료인 선박용 중유(이하 HFO) 또는 선박용 경유(이하 MGO)의 양을 계산하였다면, 이를 바탕으로 대체 연료로 전환하였을 시에 필요한 연료 양을 계산할 수 있다. 대체 연료별로 체적 에너지 밀도가 다르기 때문에 같은 거리를 운항하기 위해 필요한 연료의 양이 달라진다. 예를 들어 메탄올 연료를 사용하여 MGO와 동일한 운항을 하고자 한다면 MGO 탱크 용적보다 2.4배 크기의 e-메탄올 연료 탱크가 선박에 배치되어야 한다.
연료별 특성 비교
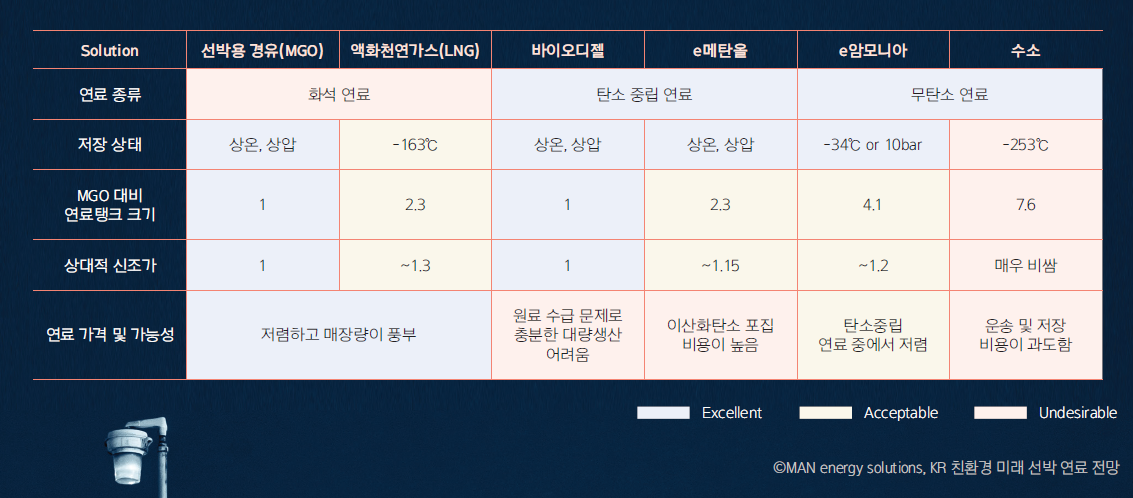
· 대체 연료 저장 장치 기술의 종류
필요한 대체 연료의 양이 결정되면 연료 탱크의 형식 및 위치를 정하여야 한다. 기본적으로 선박용 연료 저장 탱크는 일반 선체 공간을 사용하는 경우와 IMO 독립형 A형, B형, C형 그리고 멤브레인(Membrane)형 적용으로 나뉜다. 보통 필요한 연료의 양이 적은 경우, 독립형 C형 탱크가 사용되고 있으며 많은 연료가 필요한 경우, 독립형 A형, B형 또는 멤브레인형이 사용되고 있다. 다만, 메탄올 연료 탱크의 경우에는 기존 HFO 연료와 같이 일반적인 형식의 탱크 사용이 가능하므로 형상 및 탱크 크기 변화가 다른 연료 탱크에 비하여 자유롭다.
다음 그림은 대체 연료에 적용 가능한 연료 탱크의 대표적인 형식을 보여주고 있다.
대체 연료 탱크 형식 분류
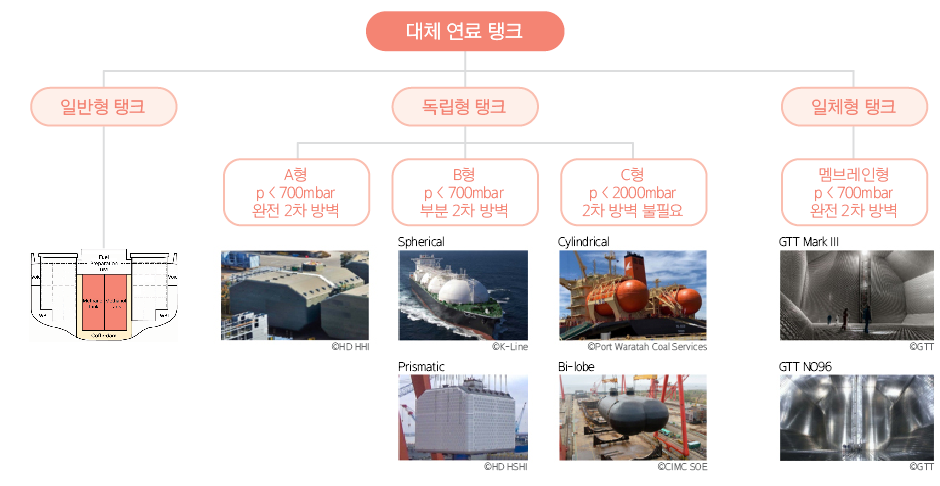
독립형 A형 탱크는 KR에서 종래에 사용되고 있는 선체강도 해석법에 따라 인정하는 기준에 의해 설계되는 탱크이다. 설계 증기압은 0.07MPa 미만이어야 하며 선체 구조와 비슷하게 설계할 수 있어 독립형 C형 탱크 대비 공간 활용의 측면에서 이점을 갖는다. 또한, 액화 연료 유출에 대하여 안정성 확보를 위해 완전한 2차 방벽이 추가적으로 요구된다. 독립형 B형 탱크는 응력 수준, 피로 수명 등을 결정하기 위해 정밀한 해석법을 이용하여 설계된 탱크이다. 설계 증기압은 0.07MPa 미만이어야 하며 부분 2차 방벽 및 누설 시 안전한 처리 및 제거를 할 수 있는 수단이 요구된다. 독립형 C형 탱크는 압력 용기 기준에 기초하며, 표면 결함이 탱크의 수명동안 탱크 외판 두께의 절반 이상 진전되지 않도록 설계된 탱크이다. 따라서, 2차 방벽의 설치가 요구되지 않는다. 멤브레인 탱크는 탱크 벽이 얇은 막으로 구성되어 액체 유출을 막고, 연료의 하중은 탱크 외측의 단열재를 통해 인접한 내부 선체가 지지하는 형태이다.
연료 탱크의 형식를 정하였다면, 연료 탱크의 위치를 선정하여야 한다. 독립형 A, B형 또는 멤브레인형의 경우, 선종 구분 없이 연료 탱크의 크기, 2차 방벽 등으로 인하여 화물구역 상갑판 하부 이외의 배치가 어렵다. 반면에 독립형 C형 탱크의 경우 상갑판 상하부 모두에 설치가 가능하지만 상대적으로 많은 공간을 차지하는 특징이 있다. 일반적인 독립형 C형 탱크의 위치로는 산적화물선의 경우 선미부 상갑판 상부, 탱커선은 화물구역의 상갑판 상부, 로로선은 화물구역 상갑판 하부 등에 고려되고 있다.
일반적인 대체 연료 탱크 형식 및 위치
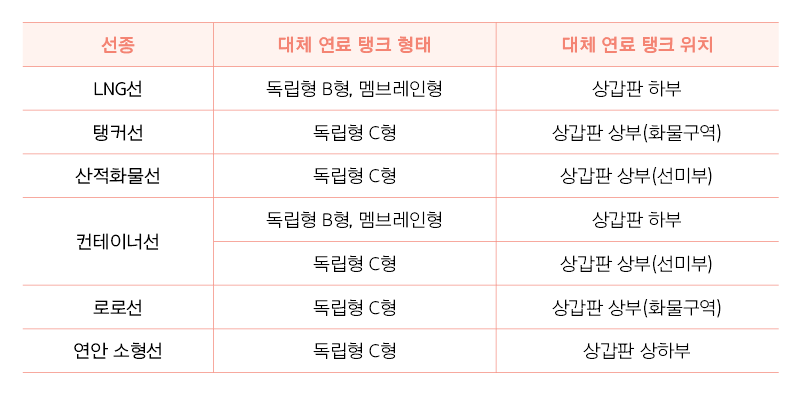
필요 용량에 적합한 연료 탱크가 호선에 배치될 수 없다면 연료 탱크의 크기를 줄이거나 기존 선체의 형상을 변경하여야 하는 경우도 발생한다. 때문에 초기 설계 단계에서 대체 연료 탱크의 위치를 고려하지 않았던 현존선의 경우, 연료 탱크 배치 문제로 인해 대체 연료로의 전환에 어려움을 겪는다.
· 대체 연료 저장 장치의 재료
연료 저장 탱크의 재료는 각각의 대체 연료 특성, 저장 설계 온도 및 설계 증기압에 의해 결정된다. 현재 가장 많은 부분을 차지하는 LNG 연료의 경우, 설계 온도는 -163도, 설계 증기압은 0.7bar 미만이 요구된다. 이에 LNG 연료 탱크 재료로는 극저온 환경에서도 강도와 인성이 저하되지 않고, 충분한 내충격성을 가져야 하므로 오스테나이트계 스테인리스강, 니켈 합금강, 알루미늄 합금강, 고망간강이 사용된다. 반면에 메탄올의 경우, 대기압에서 끓는점이 64.7도이므로 저온용 강재의 사용이 필요치 않는다. 하지만 메탄올은 일부 재료의 부식을 유발하므로 연료 탱크 코팅이라는 추가적인 조치가 필요하다. 암모니아 연료 탱크에는 통상 -55도를 견디는 저온용강을 사용하여야 한다. 액체 수소 연료 탱크의 경우 수소에 민감하지 않은 재료여야 한다.
연료 탱크의 재료를 선택함에 있어서 재료의 비용은 가장 큰 영향을 미칠 것이다. 하지만 설계를 함에 있어서 재료의 비용만큼 중요한 것은 연료 탱크의 무게이다. 각각의 대체 연료 밀도가 다르고 또한 재료 물성치 특성으로 인해 구조 강도를 만족하는 연료 탱크의 요구 두께가 달라지기 때문이다. 그로 인해 연료 탱크의 무게도 달라져 탱크 지지 구조에 추가적인 보강이 필요할 수 있다.
다음은 9% 니켈 합금강으로 제작된 LNG 연료 탱크의 무게를 기준으로, 대체 연료 밀도 변화에 따른 필요 재료 두께 및 그에 따른 연료 탱크의 무게 증가율을 나타낸 표이다.
독립형 C형 탱크의 연료 탱크 무게 증가율
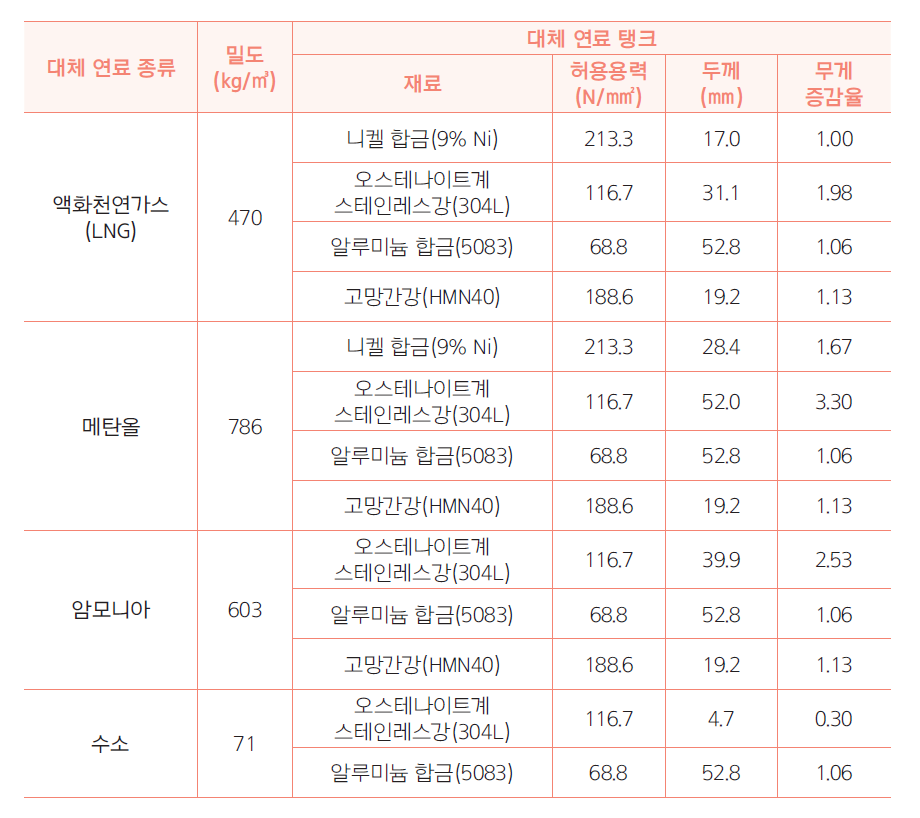
이렇듯 다양한 요소를 고려하였을 때, 단일 연료 탱크의 재료로서 LNG 연료의 독립형 A형, B형, C형 탱크의 경우 9% 니켈 합금강 또는 고망간강, 멤브레인형의 경우 오스테나이트계 스테인리스강, 또는 인바(INVAR)가 주된 방벽 재료로 사용된다. 메탄올 및 암모니아 연료의 경우 탄소망간강이, 수소 연료의 경우 오스테나이트계 스테인리스강이 주된 재료가 될 것으로 예상된다.
알루미늄 재료의 경우 연료 탱크의 무게는 9% 니켈 합금강과 크게 차이가 나지 않는다. 하지만 3배 이상의 필요 연료 탱크 두께로 인해 용접 비용 및 용접 결함 증가는 재료의 선호도를 떨어뜨린다.
다음 그림은 현재까지 설명한 필요 연료 용량에서부터 연료 탱크 형식, 연료 탱크 재료 선택의 순서를 도식화한 그림이다.
일반적인 연료 탱크 재료 분류 (1)
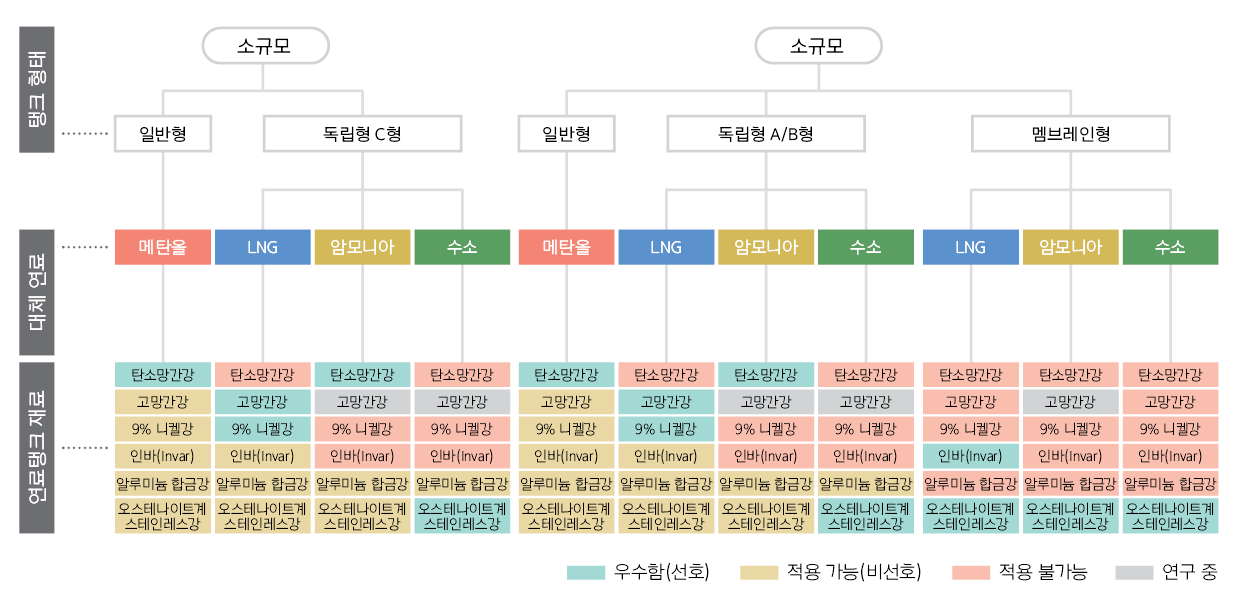
다음 그림에서는 순서를 달리하여 대체 연료별로 선호되는 연료 탱크 형식 및 연료 탱크 재료까지 나타내 보았다. 이를 참고하여 연료 전환 대비를 위해 신조 시에 어떤 연료 탱크 재료를 사용할 것인지를 중요하게 고려해야 할 것이다.
일반적인 연료 탱크 재료 분류 (2)
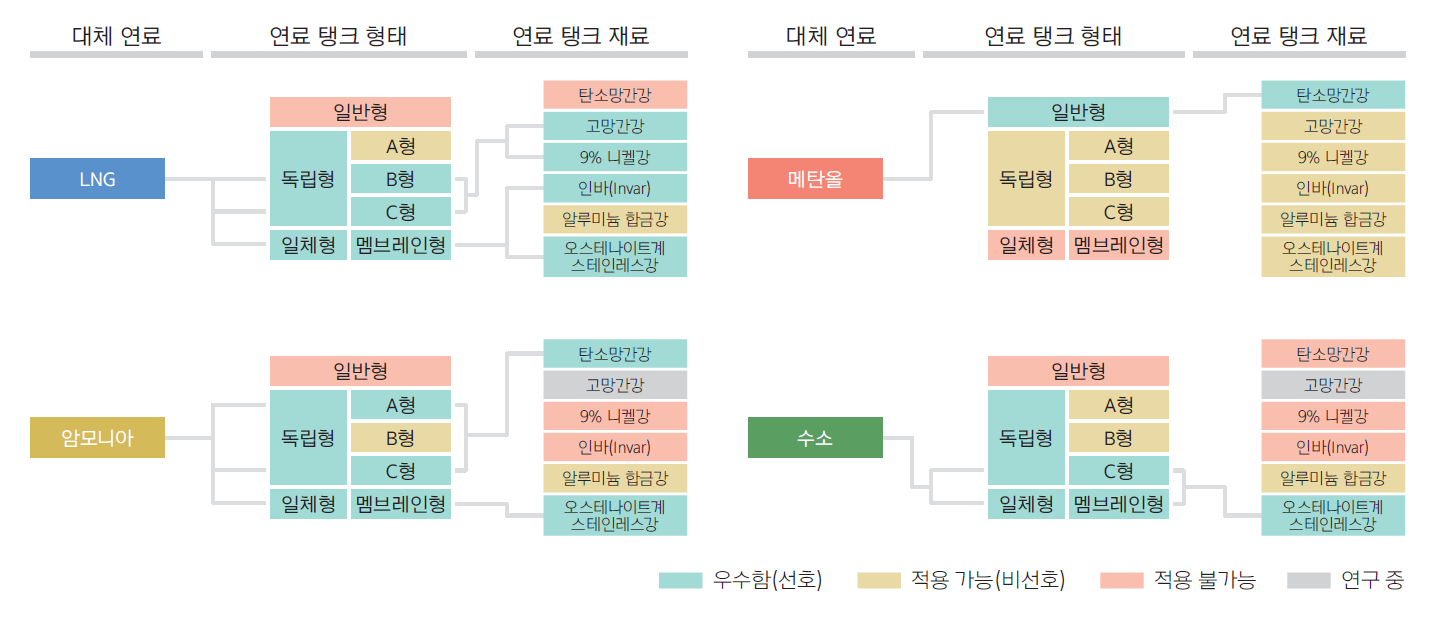
미래 대체 연료 전환을 고려한 연료 저장 장치 선택의 영향
· 컨테이너선의 메탄올 연료 추진 개조
현재 메탄올 연료의 관심도가 증가하면서 기존 연료 추진 컨테이너선을 메탄올 연료 추진 선박으로 개조하려는 계획이 늘어나고 있다. 하지만 초기에 고려되지 않은 연료를 미래에 사용하고자 개조하는 것은 상당히 어렵고 많은 투자를 필요로 한다. 메탄올 추진 컨테이너선으로의 개조는 두가지 방향성이 존재할 것이다. 기존 화물창 공간에 메탄올 연료 탱크를 삽입하여 일부를 연료 탱크 공간으로 대체하는 방법과 필요 메탄올 연료 탱크 길이만큼 선체의 길이를 연장하는 방법이다. 연료 탱크 삽입 방법은 운송하고자 하는 화물의 손실이 발생할뿐더러, 연료 탱크의 설계에 제약이 많을 것으로 판단된다. 반면에 선체 길이 연장 방법은 화물 손실의 영향은 없으나 선체 길이 연장에 따라 추가적으로 고려되어야 하는 사항이 많이 발생할 것이다. 어느 것도 쉽지 않은 작업이다.
메탄올 연료 추진 개조 예
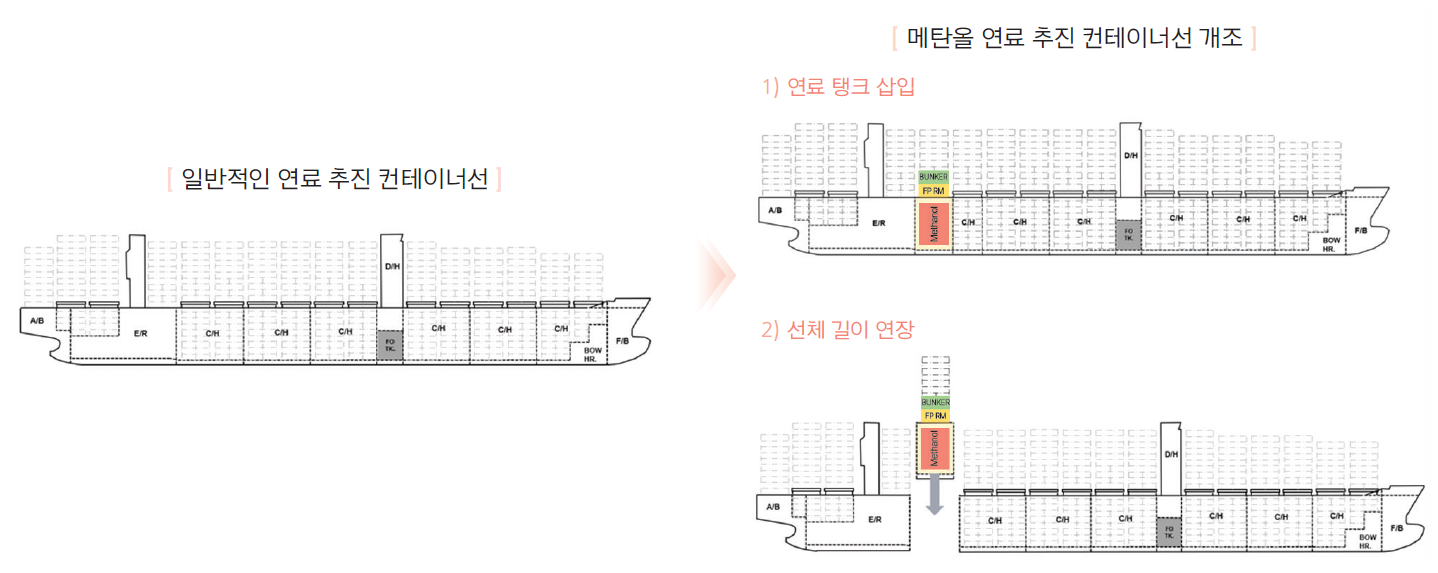
· 메탄올 연료 탱크로서의 기존 HFO 탱크 활용
지금까지 이용하던 기존 HFO 탱크를 메탄올 연료 탱크로 활용하면 안 되는 것일까? 어렵다는 것이 대부분의 의견이다. 그 이유는 메탄올의 특성과 관련이 있다. 메탄올은 일부 재료에 부식을 유발하기 때문에 탱크 코팅이 중요하다. 또한, 독성이 있어 메탄올 연료 탱크 주변에 코퍼댐*을 두어야 한다. 이 같은 메탄올의 특성을 고려하지 않고 설계된 HFO 탱크는 탱크 코팅이 안되어 있을 것이고 코퍼댐 구조도 없을 것이다. 특히 HFO 탱크의 보강재들은 탱크 내부에 위치하여 탱크 코팅의 품질을 보증할 수 없게 한다. 그렇기 때문에 메탄올 연료 준비 선박에서 HFO와 메탄올을 모두 저장할 수 있는 탱크를 설계한다면, 초기부터 코퍼댐 구조가 고려되어야 하며 탱크 코팅을 위해 보강재가 탱크 바깥 쪽으로 배치되거나 파형 격벽(Corrugated Bulkhead)으로 연료 탱크를 형성하여야 한다.
* 코퍼댐 : 양측의 구획이 공통 경계를 갖지 아니하도록 배치된 빈 공간
HFO와 메탄올 연료 탱크 설계 예
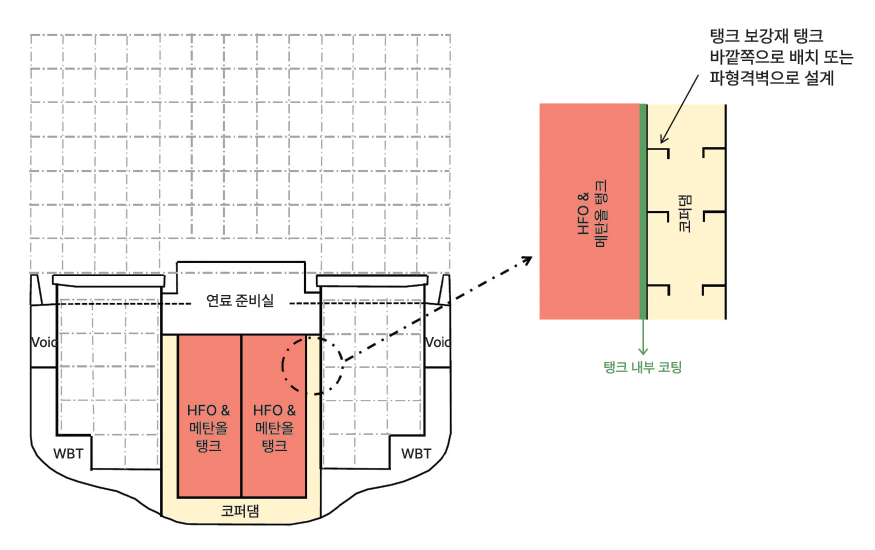
· 연료 저장 장치가 개조 비용에 미치는 영향
앞서 언급했듯이 초기에 고려치 않았던 연료 추진 선박으로의 개조는 상당한 비용과 시간이 요구된다. 연료 전환 개조에 대한 연구 보고서 등을 참고하게 되면 선종마다 개조 비용이 다양하지만, 적게는 선가의 50%, 많게는 100% 이상까지 개조 비용이 소요된다는 연구 결과도 있다. 또한 4~6개월의 기간 동안 개조가 이루어지면서 운임 손실도 발생한다. 이런 사항들 때문에 현재 운항 중인 선박을 대체 연료 추진 선박으로 개조하는 것은 현실적으로 어려움이 많다. 대체 연료 준비 선박이 많아지는 이유 중 하나도 바로 대체 연료 추진 선박으로의 개조 비용을 줄일 수 있기 때문일 것이다.
결론 : 연료 저장 장치 기술의 중요성
탈탄소화 요구에 따른 대체 연료로의 전환, 연료 저장 장치의 영향에 대해서 살펴보았다. 성공적인 대체 연료로의 전환에 있어 연료 저장 장치는 그 영향력이 매우 크며 중요하다. 이미 LNG 추진 선박이 도입되기 시작한 때부터 당장이 아닌, 미래 시점에서의 연료 전환 계획이 반영된 대체 연료 준비 선박도 도입되어 왔다. 하지만 현재까지 대체 연료 준비 선박의 실질적인 효과에 대해서는 대부분 회의적인 것이 사실이다. 불확실한 미래 사항을 신조 단계에서부터 당장 결정하고 투자한다는 것에 어려움이 크기 때문일 것이다. 하지만 신조 선박뿐만 아니라 운항 중인 선박의 연료 전환을 고려하지 않으면 안 되는 해운 탈탄소화의 요구가 다방면에서 점점 거세지고 있다. 해운선사, 조선사, 에너지기업 등 다양한 분야에서 연료 저장 장치에 대한 더욱 실질적인 논의가 이루어져야 하며, 협력을 통해 현실적인 해결책과 전략들을 찾아가야 할 것이다. 이 글이 그런 논의를 위한 작은 시작점이 되었으면 좋겠으며, KR도 그런 논의와 협력에 기여할 수 있었으면 한다.

CCUS 산업과 LCO₂ 운반선 기술
![]() KR 탱커팀 이동범 책임 |
LCO₂의 안전한 운송을 위해
|
CCUS 기술과 탄소중립 노력
온실 가스 배출량의 증가에 따른 지구 온난화가 기후 변화와 같은 심각한 문제를 야기하고 있다. 이에 많은 국가와 기업들이 탄소중립을 실현하기 위한 노력을 강화하고 있는데, 탄소 포집·활용 및 저장(CCUS) 기술은 이러한 노력의 일환으로 주목받고 있으며 그 성장세가 두드러지고 있다.
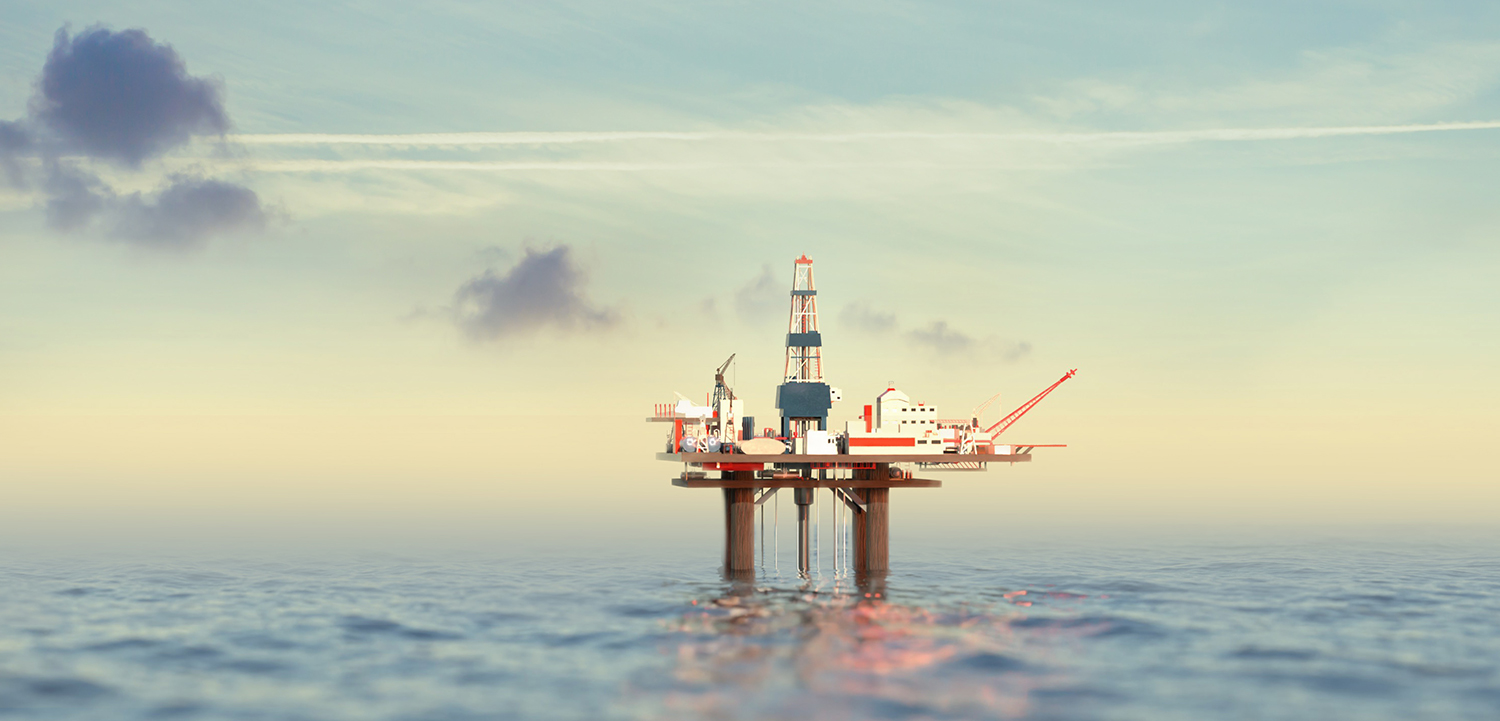
CCUS 산업과 이산화탄소 운반선의 역할
CCUS 산업의 성장으로 인해 이산화탄소 운반선에 대한 수요 또한 급증하고 있다. 이산화탄소 운반선은 CCUS 공정에서 포집된 대량의 이산화탄소(CO₂)를 저온·고압의 안정적인 액화 상태로 저장소까지 안전하게 이송할 수 있도록 특별하게 설계된다.
이산화탄소는 실온에서 기체 상태로 존재하지만, 대량 운송을 위해서는 저온과 고압 조건에서 액체 상태로 유지되어야 하므로 IMO C 타입 탱크가 적용되어야 한다. 효율적인 운송을 위해 이산화탄소 운반선은 기체, 액체, 고체의 세 가지 상태가 함께 존재할 수 있는 온도와 압력인 삼중점에 인접한 조건에서 운송이 가능하도록 설계되어야 하며, 운항 중에는 이산화탄소의 상 변화가 발생하지 않도록 각별한 주의가 요구된다.
한편, IGC 코드에서는 CO₂를 질식성 화물로만 분류하고 있으나, 다수의 국가에서 CO₂를 독성 물질로 정의하고 있음을 고려하여 국제해사기구(IMO)에서도 이에 대한 논의를 시작하였다. CO₂가 독성 화물로 분류되는 경우, 독성 화물의 운송·저장·취급과 관련한 IGC 코드상의 다양한 안전 요건들을 추가로 적용받게 된다. 다만, CO₂의 독성은 다른 독성 화물에 비해 심각도가 크지 않으므로 일부 규정은 면제가 가능할 것으로 예상되는 바, 향후 국제해사기구의 논의 결과를 주목할 필요가 있다.
액화 상태의 이산화탄소(CO₂)를 안전하게 운송하기 위한 탱크 설계에는 다음과 같은 다양한 요소가 고려되어야 한다.
액화 이산화탄소 운반선
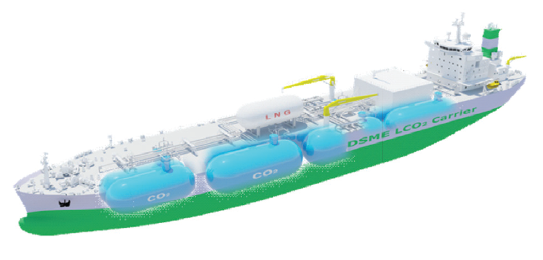
이산화탄소 운반선 설계 요소
· 화물 탱크의 압력
탱크의 설계 압력은 저압과 중압으로 나뉜다. 저압과 중압은 운반되는 화물의 양, 최종 저장소까지의 거리, 포집된 CO₂의 불순물 수준 및 상태 등 여러 요인에 따라 결정된다. 탱크의 운용 여유 측면에서는 중압이 저압에 비해 유리한 장점이 있다. 하지만 탱크 설계 시 압력의 증가는 탱크 두께의 증가로 이어지는데, 화물 탱크의 강재 두께 제한으로 인해 중압의 경우 대형화가 힘들다는 단점이 있다. 이에 비해 저압의 경우 탱크의 대형화가 가능하지만, 삼중점에 근접한 운용 압력 때문에 중압에 비해 압력 변동에 의한 고체화(드라이아이스화) 위험성이 커지므로 정교한 압력 제어 및 설계를 포함한 대책 수립이 필요하다.
이산화탄소 저장 탱크의 압력과 온도 설정
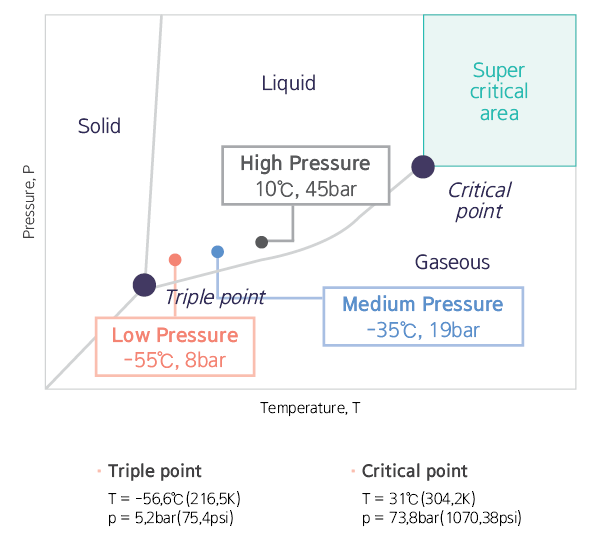
· 화물의 온도
이산화탄소는 저압에서는 -55도, 중압에서는 -35도의 저온으로 운반된다. 따라서 IGC 코드에 따라 저온에 맞는 탱크 재질을 선택하는 것이 중요하며, 탱크의 수축과 팽창에 따른 열응력을 최소화하기 위한 탱크 설계가 필요하다.
· 이산화탄소의 밀도
이산화탄소의 밀도는 약 1.15 ton/m³으로 일반적인 LPG에 비해 약 2배 높은 밀도이다. UI GC7에 따라 피로 측면에서의 추가적인 검토가 요구되며, 슬로싱 측면에서도 높은 비중을 고려한 검토가 요구된다.
· 이산화탄소의 순도
이산화탄소는 순도에 따라 증기압이 크게 변화한다. 일반적으로 이산화탄소 운반선 설계 시에는 고순도의 이산화탄소 운반을 조건으로 하는데, 순도에 따른 증기압의 변화까지 반영할 경우 더 높은 증기압에서의 저장이 가능하도록 설계해야 한다. 이산화탄소의 수분 함량은 탱크의 부식에도 영향을 미치므로 주의가 필요하다.
· 화물 탱크의 강재 두께
현재 IGC Code에서는 40mm까지의 강재 두께를 인정하고 있다. 단, IACS UR W1은 독립형 Type C 탱크의 경우 40mm 초과-50mm 이하의 강재에 대해 용접 후 열처리(PWHT, Post Weld Heat Treatment) 또는 ECA(Engineering Critical Assessment)를 요구하고 있다. 대형 탱크의 경우 용접 후 열처리가 쉽지 않으므로 ECA가 적용될 가능성이 높으며, 이를 감안해 IACS에서는 프로젝트 팀을 구성하여 ECA 수행 절차를 마련할 예정이다.
· 화물 탱크의 형상
탱크의 형상에 있어서는 제작 및 설계의 용이성을 고려하여 Cylinder 형태의 Type C 탱크를 사용할 수 있다. 더불어 제작 및 설계의 어려움은 있지만 공간 활용에 용이한 Multi-lobe 형태의 Type C 탱크를 사용할 수도 있다.
LCO₂ 운반선의 암모니아 혼적 시 고려사항
최근 암모니아·LCO₂ 겸용 운반선 개발 기사를 종종 접할 수 있다. 암모니아를 화력 발전소로 운송한 후, 화력 발전소에서 배출되는 이산화탄소를 저장소로 운송하는 것은 선박 운용의 효율성 측면에서 매우 이상적이다. 이 경우 가장 중요하게 고려되어야 할 요소는 암모니아 운송 후 암모니아 잔류물과 이산화탄소의 혼합으로 인한 이산화탄소의 순도 변화이다. 암모니아를 하역 후 이산화탄소 선적 시 완벽한 탱크 세척이 이루어지지 않는다면 이산화탄소의 순도에 영향을 줄 것이고, 이는 화물의 증기압 변화로 이어져 심각한 사태를 초래할 수 있기 때문이다. 화물 하역 시스템(Cargo Handling System) 또한 완전한 세척이 요구되며, 이를 위해 각각의 암모니아와 이산화탄소를 분리 이송하는 화물 운송 시스템이 필요할 수도 있다. 따라서 동일 탱크에서의 암모니아 및 액화 이산화탄소 교차 적재는 현실적으로 쉽지 않은 과제가 될 것이다.
KR의 역할
최근 KR은 여러 조선소들과의 협력을 통해 이산화탄소 운반선의 화물 탱크 및 화물창에 대한 구조적인 안전성 및 적합성 검증을 완료하였다. 화물 탱크는 IGC Code에서 요구하는 영구 하중, 기능 하중, 환경 하중 및 사고 하중 등 다양한 하중 조건에 대한 구조해석을 거쳐 구조적인 안전성이 확인되었으며, 화물창 및 탱크 하부 지지 구조 역시 다양한 설계 하중 조건 하에서의 구조 신뢰성이 검증되었다. KR은 이러한 긴밀한 협력을 통해 탈탄소화 시대에 맞춰 새로운 영역을 개척해가는 고객들의 신뢰할 수 있는 파트너가 되고자 한다.
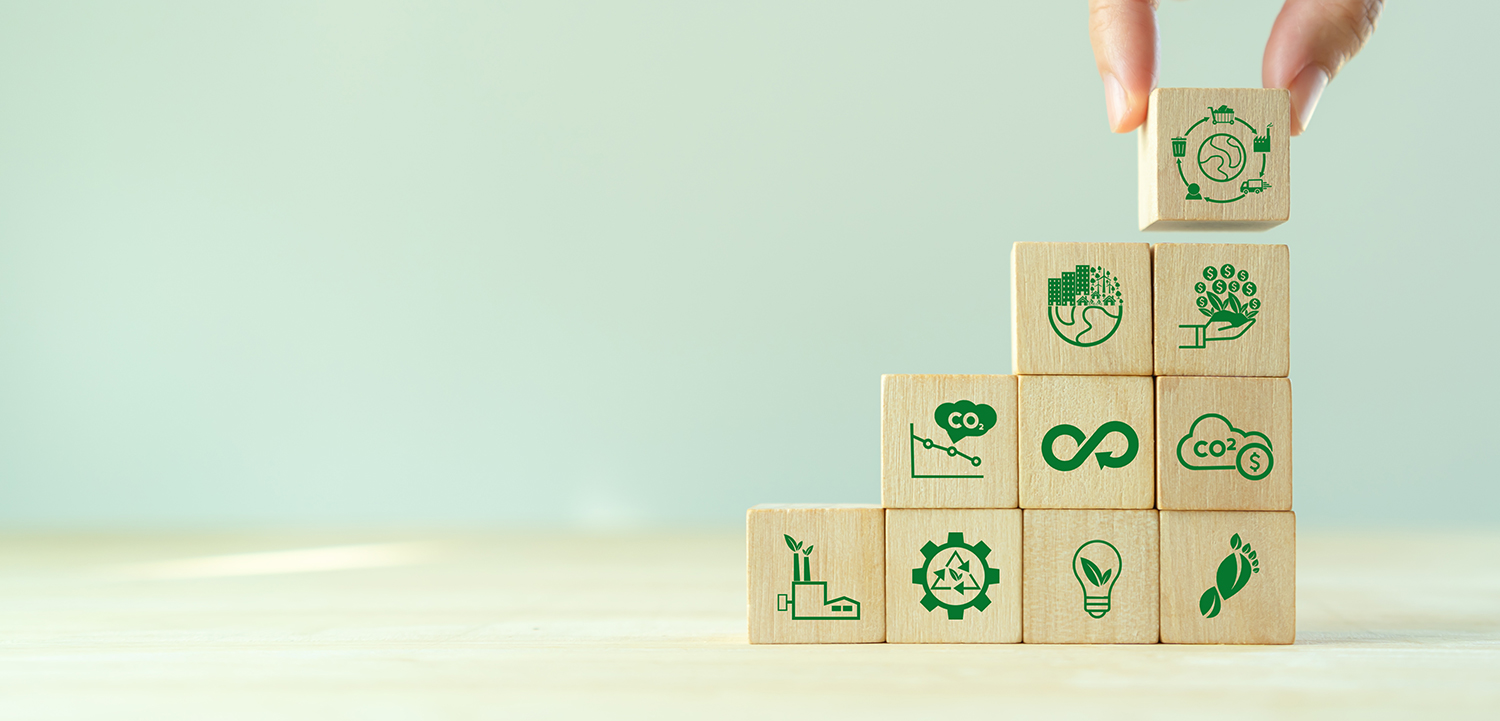