Insights
KR Decarbonization Magazine
VOL.02 | SPRING 2023
Economic Analysis of Ships using Alternative Fuel
– A Case Study
![]() KU Kyojun, Surveyor of KR Business Support Team |
Leading the way in the decarbonization era:
|
The next ship fuel choice for a greener future
Starting with AP Moller-Maersk's order for methanol-fueled container ships, competition for greener ships has intensified as CMA CGM, COSCO, and HMM have placed orders for methanol-fueled container vessels. Methanol is emerging as a next-generation alternative fuel that emits less greenhouse gas from ships than conventional fuel and is cheaper than LNG-fueled ships. However, from a life cycle assessment (LCA) perspective, grey methanol emits more greenhouse gas(GHG) emissions than conventional fuels. Therefore, securing a green methanol supply chain is likely to be the main objective for methanol-powered ships.
LNG is currently the most widely used alternative low-carbon fuel that emits fewer GHG emissions from ships than conventional fuel oil and methanol. However, when an LNG-powered ship is in operation, a methane slip occurs where methane, the main component of LNG, is incompletely burned and escapes into the atmosphere. Methane is a GHG with a higher greenhouse effect than carbon dioxide, so it is vital for LNG-powered ships to solve this methane slip issue. In addition, to use LNG as a fuel, it must be kept in a cryogenic state, which adds to the cost of new builds.
It has been a decade since LNG was first used as a marine fuel, and the supply chain and infrastructure have been established, but there are still some shortcomings. Recently, there has been increased interest in methanol as a marine fuel, but it will take time to build the supply chain and infrastructure. As engine development progresses, ammonia is predicted to be as attractive an alternative as methanol. However, it is expected that ammonia will be used as a marine fuel after 2025.
This makes it difficult to predict which fuel will be dominant in the future. It is important to continuously analyze which fuel will be the most cost-effective option and find the optimal solution. Although there is no clear answer, an economic analysis of shipbuilding and operation from the perspective of future fuels can provide a minimum basis for decision-making.
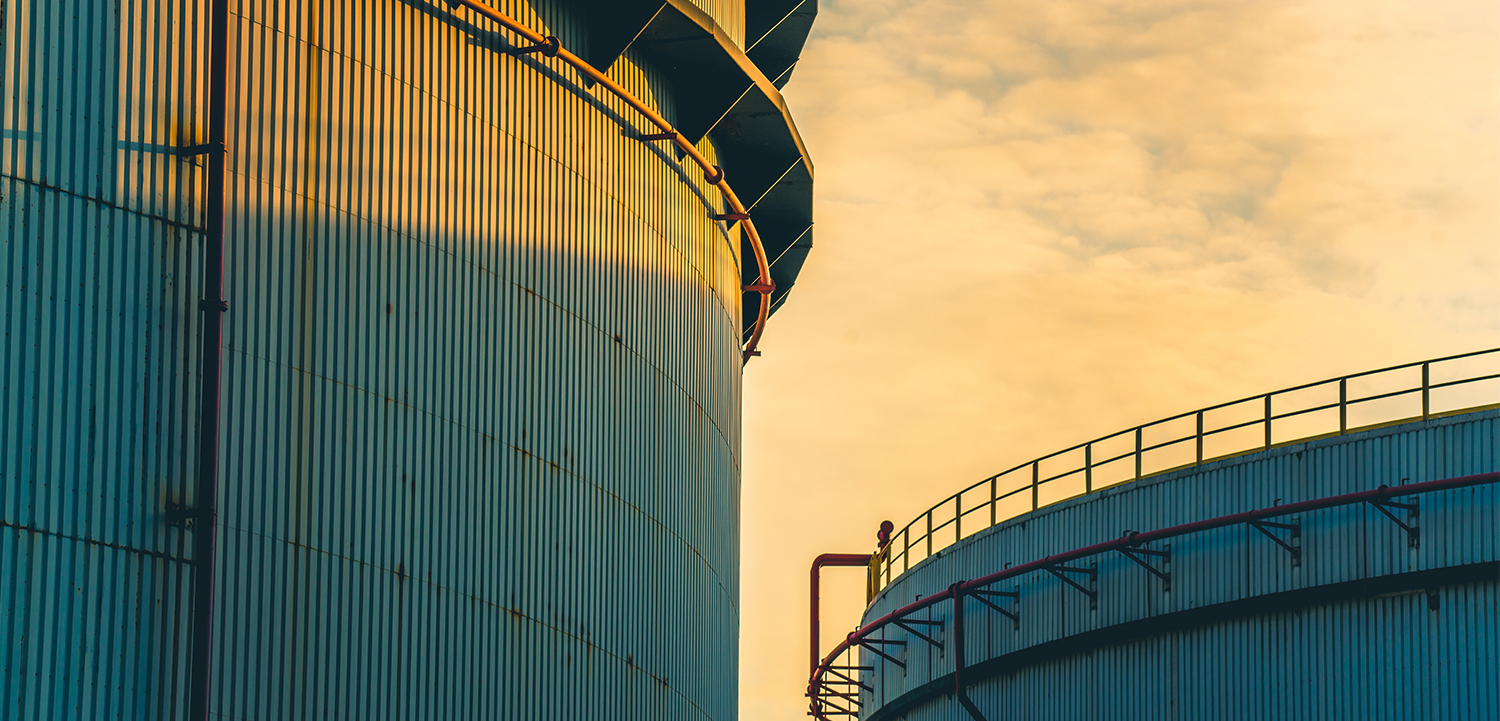
Optimal economic analysis by comparing CAPEX and OPEX
To analyze the economic feasibility of each fuel, the costs incurred up to 2050 were compared for container ships that have recently been ordered in large quantities. The fuels compared were HFO, LNG, methanol and, after 2030, carbon neutral fuels such as biofuels and e-fuels. In addition, depending on the fuel used, the cost of retrofitting the ship was considered where necessary. Two factors were considered in the economic analysis: CAPEX, which included the price of newbuildings and conversions, and OPEX, which included the cost of fuel for operation, environmental regulations, and the loss of containers to free up space for fuel tanks.
Factors for Economic Analysis
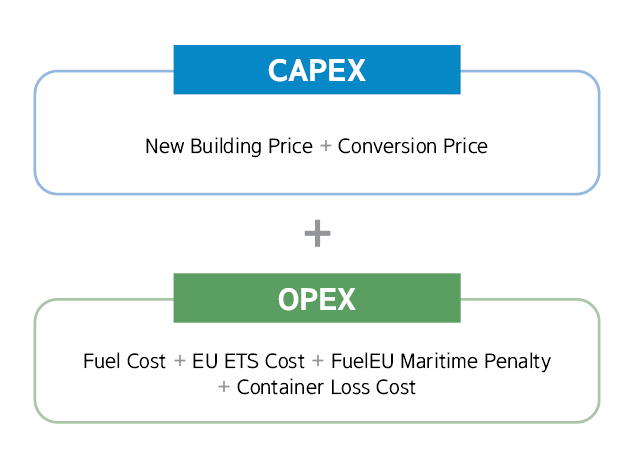
Estimated fuel price, considering environmental regulatory costs
Fuel cost is the most significant element of the items considered in the economic analysis. In this respect, the fossil fuels currently used by most ships, have a significant cost advantage. However, the use of fossil-based fuels is expected to gradually decrease as the industry works to reduce GHG emissions and as environmental regulations become more stringent.
Taking into consideration the impact of environmental regulatory costs, biofuels and e-fuels, which are considered sustainable fuels, are expected to become more competitive than fossil fuels after 2040. Prices remain high for biofuels and e-fuels at present, due to production costs and supply problems. Therefore, long-term investment and support for biofuels and e-fuels are needed.
It is difficult to predict the price of fuel due to various uncertain factors. To minimize these uncertainties, price variability was considered by dividing the expected prices of each fuel into maximum, minimum and average. The environmental regulatory costs of EU Fit for 55 were also analyzed. EU Fit for 55 is a regulatory package aimed at achieving the reduction targets of EU climate legislation, which aims to reduce GHG emissions and switch to low-carbon fuels through the EU ETS and FuelEU Maritime. As a result, fossil-based HFO and LNG fuels are competitive until 2030, but fuels such as bio-LNG, bio-methanol and e-ammonia are expected to dominate after 2040.
Environmental Regulations and the Outlook for Marine Fuel Costs
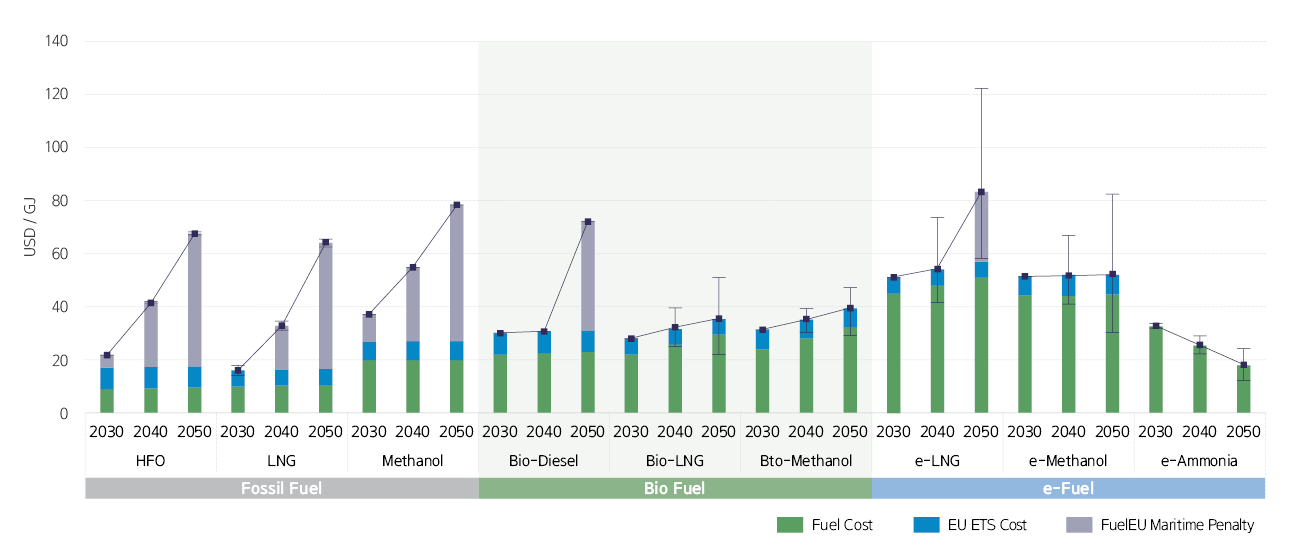
The EU Fit for 55 legislation precedes the IMO’s mid-term measures to reduce GHG emissions. It currently applies to ships entering EU countries but may be extended to the IMO mid-term measures in the future. EU ETS will be implemeted in 2024 and FuelEU Maritime in 2025, and as corresponding IMO mid-term measures, the Emission Cap-and-Trade System(ECTS) for economic measures and the Greenhouse Gas Fuel Standard(GFS) for technical measures are under discussion.
IMO Mid-term Measures
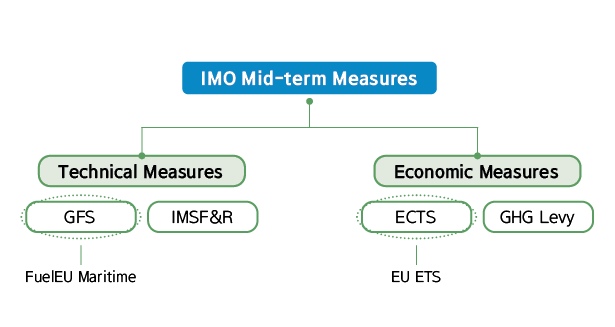
The most economical option
Based on the estimated fuel costs up to 2050, the economic feasibility of operating an 8,000 TEU container ship was compared in a total of 23 cases. It was concluded that LNG-powered ships would be the most economical option, especially if HFO fuel is used before 2030 and fossil-based LNG fuel after 2030. Although LNG fuel has the disadvantage of methane slip problems and high ship prices, it is currently the most advanced alternative fuel due to its low fuel costs. However, if the price of LNG fuel rises temporarily, as it has in recent years, flexible operation with HFO fuel will be required.
Ships using conventional fuels will incur high environmental regulatory costs if they continue to use HFO fuel, so measures such as using biodiesel fuel or converting to other alternative fuel sources should be prepared. If future environmental regulations are tightened, the use of biofuels and e-fuels will be further enforced.
In the case of methanol-powered ships, the economic feasibility was generally ranked lower due to the high price of green methanol fuel. However, methanol-powered ships have a lower newbuilding cost than LNG-powered ships, so it is anticipated that many shipowners will choose methanol-powered ships. As a result, the price of green methanol will fall as the infrastructure and supply of green methanol fuel increases. If the price of bio-methanol is more than 28% lower than the current forecasted price, methanol-powered ships may be the most economical option.
Future Fuel Economic Analysis of Newbuildings and Operations
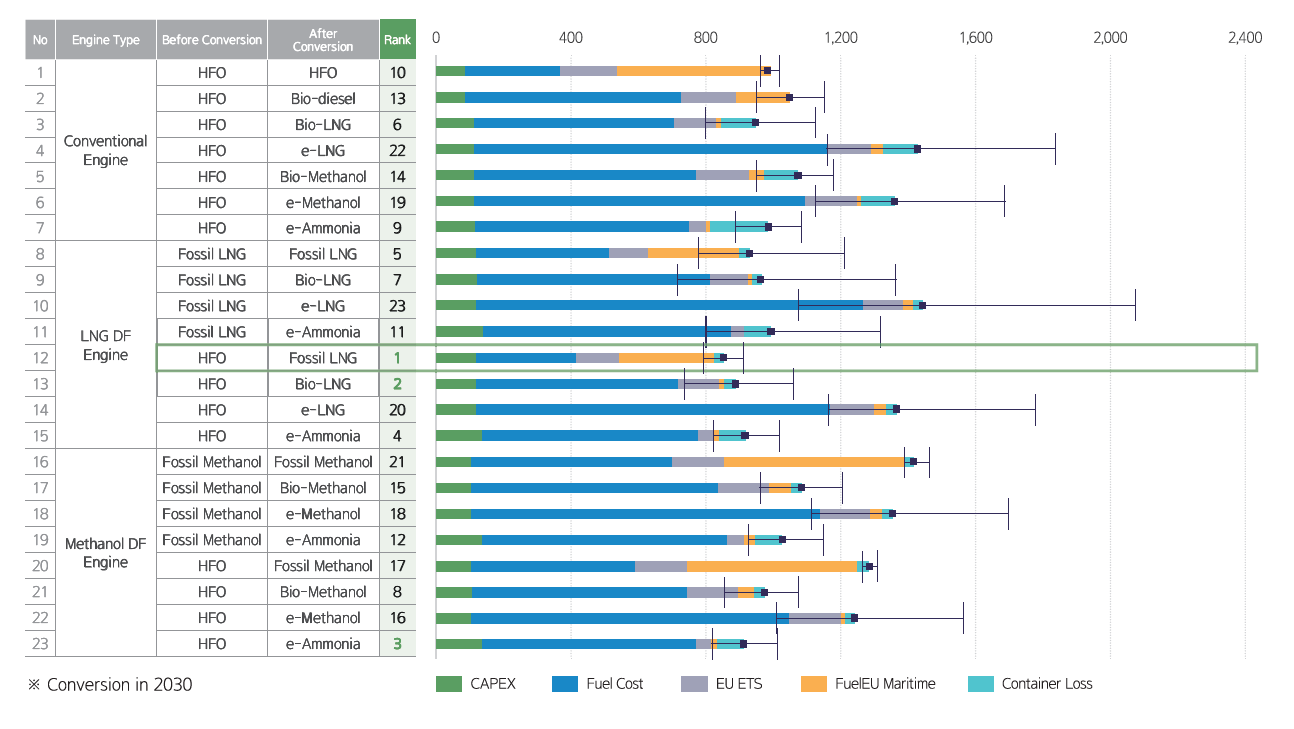
The results of the economic analysis may vary for different sizes or types of vessel. In addition, the results of the economic analysis cannot provide an absolute answer to the decision, as uncertainties remain despite the various factors considered. To overcome uncertainties, it is important to analyze the available information as much as possible, and cooperation between related industries is necessary.
KR has laid the foundation for analyzing the economic feasibility of ships according to the use of alternative fuels and plans to explore the economic feasibility of other ship types and sizes in the future. Furthermore, various cooperation from members of the shipping industry interested in analyzing the economics of alternative fuels for ships, future data can be improved. Through such collaboration, we hope to lead a successful decarbonization journey together.
Can the Toxicity of Ammonia be Overcome When Used as a Ship Fuel?
![]() CHOI Wooseok, Principal Surveyor of |
Effective and enforceable safety regulations,
|
Safety concerns regarding the use of ammonia as a ship fuel
New alternative fuels or emission reduction technologies are being developed to meet the IMO GHG Strategy, and ammonia is recognized as one of the most promising fuels as a carbon-free form of energy. However, there are still uncertainties about the use of ammonia as a ship fuel, and toxicity is the most questionable factor in whether ammonia will become a mainstream marine fuel in the future. The use of toxic gas as a shipping fuel is unprecedented, and is prohibited under the IGC Code and MARPOL Annex VI/18.
The new challenge of using toxic gas as a ship’s fuel raises the question of whether it is possible to completely control the leakage of ammonia from the ammonia facility installed on the ship. Another question is - if it is not possible to have complete control of the leakage - is it possible to protect the crew from the leakage? This is because ammonia can be fatal to humans, even at low concentrations.
On the other hand, some claim that ammonia can be used safely as a ship fuel, based on experience with the use of ammonia in land-based industries and the transport of ammonia cargoes by ship. While this is also a possibility, it is not so easy to jump to conclusions as there are distinct differences between land and marine environments, the ammonia cargo systems and the ammonia fuel systems as outlined below.
Risks of using ammonia as a marine fuel
· Ships have limited space compared to land-based systems, so there are restrictions on evacuation when a leakage happens. There is no external support available to assist with an accident, so incidents need to be handled by onboard crew.
· Cargo ammonia is isolated in the cargo tank during ship operation, but fuel ammonia flows into the engine room during ship operation, and the ammonia is burned in the engine. This means there is a greater possibility of crew members being exposed to ammonia.
To safely use ammonia as fuel, it is necessary to identify all possible leakage scenarios that may occur on a vessel. Based on the identified scenarios, a ship needs to be prepared with safe equipment and aligned to prevent a dangerous situation. This raises the question on whether safety measures for potential leakage scenarios would be effective in the limited space onboard a ship.
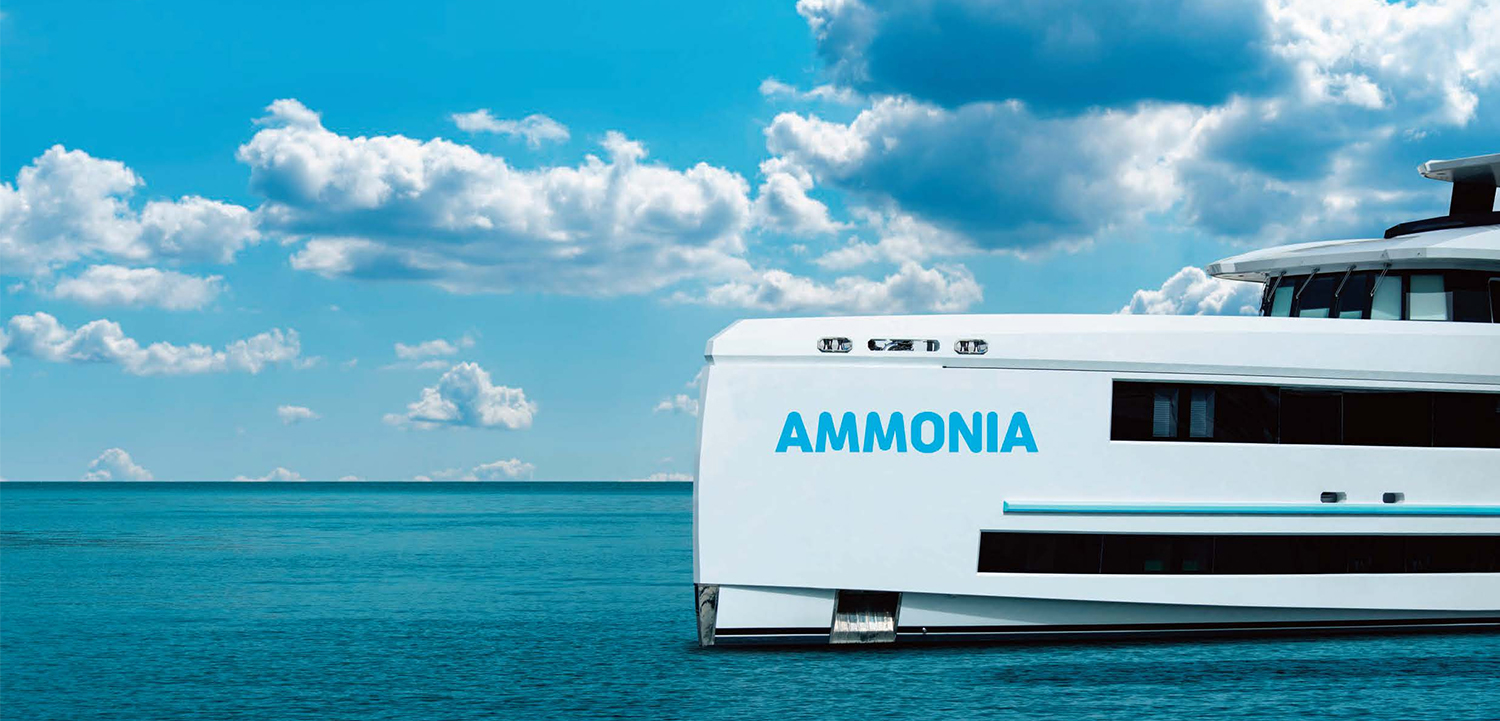
Measures to protect seafarers from ammonia gas
The concept design of the ammonia engine and fuel supply system is proposed by the manufacturer, and the concept is similar to that of low flash-point fuels. Based on this design concept, all possible leakage scenarios can be identified. Safety measures for leakage scenarios should be based on the concentration for toxicity as well as the concentration for flammability (LEL). The permissible exposure limit, which is the concentration that does not affect health, should be determined, taking into account the duration and the frequency of exposure. Concentration reference values already exist for various exposure conditions on land, and concentration reference values under conditions similar to the exposure environment of vessels can be applied to ships. The exposure limit value of 25 ppm (PEL-TWA by NIOSH), which does not result in serious health effects after repeated exposure for 8 hours, is being discussed as a possible value for the permissible exposure limit reasonable to apply to ships. In addition, the concentration that causes serious health effects even after short-term exposure should be determined to prevent detrimental exposure on board a ship. It is reasonable to set the AEGL-2 concentration at 220 ppm.
Assuming the above concentrations are applied to ships, how can long-term exposure to an ammonia concentration of 25 ppm and short-term exposure to 220 ppm be avoided? The simple answer to this question is that a gas detector installed in a hazardous gas environment will sound an alarm at 25 ppm ammonia, shut down fuel systems at 220 ppm and activate gas treatment systems.
The characteristics of each leakage scenario, including the amount of leakage, can be inferred from the design. The safety of seafarers can be ensured by taking the following safety measures for major sources of leakage:
· The machinery space can be implemented as a complete gas-safe space by applying the concept of gas-safe machinery space in the IGF Code. In this case, gas detection in a double-walled pipe shall activate an alarm at an ammonia concentration of 25 ppm and shut down fuel systems at 220 ppm.
· In the fuel preparation room and the tank connection space, the gas detector in the space will activate an alarm at an ammonia concentration of 25 ppm, shut down the fuel systems and activate the gas treatment systems at 220 ppm. This limits the gas concentration in the space and the gas concentration of the ventilation to the open deck.
· During bunkering, access to the hazardous area around the bunkering station shall be prohibited. The gas detector around the bunkering manifold will activate an alarm at an ammonia concentration of 25 ppm, activate gas treatment systems to limit the gas concentration and shut down the bunkering operation.
· Ammonia leakage into the air during purging of the fuel pipe should be limited to 220 ppm by the ammonia treatment systems.
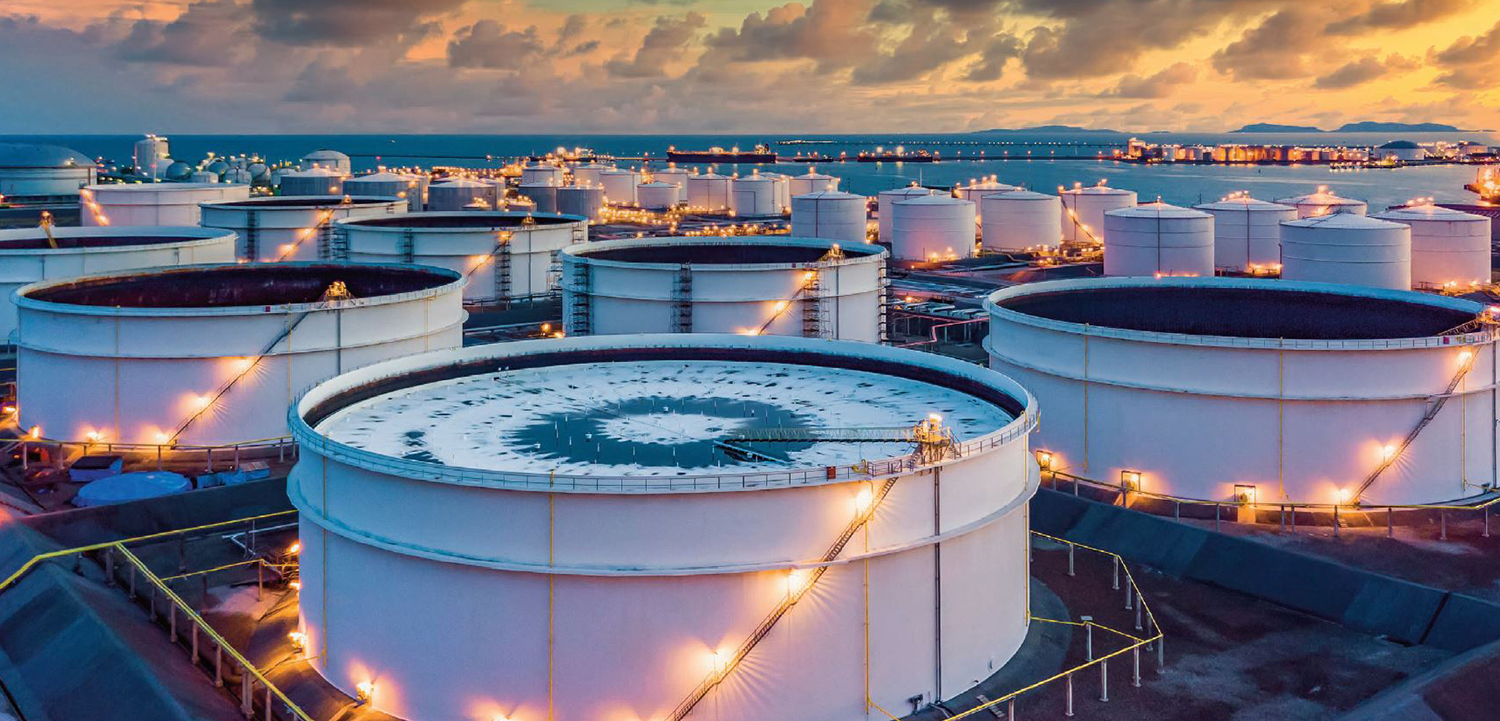
For the leakage scenario during normal operation, as described above, the valid gas treatment systems can remove the ammonia gas to the permissible exposure limit. However, in an emergency, if the pressure relief valve of the tank is opened due to a fire or collision around the tank, a large amount of leakage may occur. This could be prevented by protecting the tanks against collision and fire. In addition, feasible gas treatment systems shall be installed, and an effective emergency response plan shall be established for the emergency case.
Toxic zones shall be defined for all release gas sources, and the gas-safe area shall be located away from the toxic zone and isolated to prevent ammonia gas from flowing into the gas-safe area. The ammonia toxic zone should be defined as the 25 ppm limit.
In addition to the above, there are many other toxicity safety issues that need to be considered in detail. However, the protection of seafarers from hazardous concentrations of ammonia gas can be achieved through these measures.
Development of safety provisions
Whereas the safety regulations for fuels have so far only dealt with flammability, the toxicity of ammonia must be dealt with in addition to its flammability. For the new hazard characteristic of toxicity, an acceptable level of safety must be agreed. The functions required for ships to meet this level of safety will then be defined. Finally, detailed requirements for the implementation of the functions will have to be developed.
The IMO has started to develop the safety provision for ammonia fuel from the 8th CCC and is accelerating the work with a plan to complete the development in 2024 and adopt the interim guidelines in 2025. During the development process, the focus is on ensuring safety against the toxicity of ammonia, and Member States and industries in various fields are raising issues on risks and sharing opinions on ensuring safety. In addition, it has been decided to develop standards for the discharge at sea of ammonia bilge, which is generated during the treatment of ammonia gas, in cooperation with the MEPC.
While the safety regulation for ammonia fuel is being developed as the IGF Code, it is expected that the safety regulation for ammonia cargo as fuel (IGC Code) will be developed based on the IGF ammonia fuel safety regulation when it is finalized. As in the case of LNG and LPG fuel, the first application of ammonia fuel is expected to be an ammonia carrier, which is more straightforward than an IGF ship. Therefore, along with the development of the safety provisions for IGF ammonia fuel, the development of the safety provisions for IGC ammonia fuel should also be carried out as a matter of urgency.
A safety provision shall ensure the effectiveness and feasibility of safety measures. This means that the required safety measures must be effective in eliminating the risk and feasible to implement on the ship. To this end, it is essential to obtain opinions from various fields related to ammonia fuel, such as ammonia chemists, ship operators, shipbuilders and safety experts, in the process of developing the safety provision. KR is closely working with ammonia fuel experts across various fields to develop ammonia fuel regulations that ensure effectiveness and feasibility.
The era of ammonia fueled ships is not far away
The IMO Interim Guidelines for Ammonia Fueled Ships are expected to come into force, and the development of ammonia engines will be completed by 2025. In addition to safety provision and technology development, human factors such as crew training, maintenance and inspection of ammonia equipment and operating manuals are also important for the safe use of ammonia as a ship fuel. There are industry concerns surrounding the safety of ammonia-fueled ships. However, just as the safety concerns over the use of low flashpoint fuels were overcome in the past, the use of toxic fuels will likewise be overcome through cooperation between regulators and industry. With confidence, ammonia can be safely used as ship fuel.
CCS and CO₂ Carrier Technology for the Carbon Neutral Era
![]() Professor SEO Yutaek, Department of Naval Architecture and Ocean Engineering, Seoul National University |
Close collaboration between different sectors is
|
The rise of CCS technologies in the energy transition
As governments around the world continue their efforts to tackle climate change, new regulations are being introduced, and the maritime industry is striving to respond. The shipping industry is struggling to cope with the business changes brought about by the introduction of regulations such as Fit for 55 and FuelEU Maritime. It is facing challenges with no apparent solutions, such as green fuels and Life Cycle Assessment of marine fuels. These changes are occurring across all industries and may present new opportunities for the shipping industry. The rapid increase of LNG in the energy sector has led to orders for LNG carriers, so it is worth paying close attention to the impact of carbon neutrality efforts in the energy industry on shipping.
Carbon neutrality and decarbonization have changed the way energy companies do business. Some companies have announced plans to produce renewable energy, such as offshore wind, or to switch to carbon-free energy sources, such as hydrogen and ammonia. Leading energy companies such as BP, Total, Shell, and ExxonMobil have announced plans to build hydrogen production plants and invest in offshore wind. Interestingly, while their proposed hydrogen economy envisages green hydrogen, the current state is such that natural gas and blue hydrogen are expected to play the bridging role, requiring large amounts of CO₂ to be treated during blue hydrogen production. Not surprisingly, large-scale Carbon Capture and Storage (CCS) projects are ongoing worldwide.
Global CCS project status and CO₂ transport, storage and infrastructure needs
The Northern Lights project in Norway is currently the most high-profile CCS project. It is billed as the world's first open-source CO₂ transport and storage project, with partners including Equinor, Shell and Total. The plan is to transport CO₂ from domestic sources to aquifer storage site by ship, with two vessels currently under construction and a target injection of 1.5 million tonnes of CO₂ per year by 2024. The opening up of injection sites to both domestic and foreign CO₂ sources has attracted considerable attention from European companies.
The Dutch Porthos project will receive CO₂ via pipeline from domestic CO₂ sources, store it at a hub in Rotterdam and inject it into a depleted gas field 20 kilometers off the Dutch coast. EBN, the Dutch gas company, is the key player in the project and aims to inject 2.5 million tonnes of CO₂ per year from 2026.
The Bayu-Undan CCS Project in Australia, led by Santos, will capture CO₂ from the Darwin LNG plant and inject it into a depleted gas field via a 500km pipeline. Santos is also working on a CCS project at the onshore Moomba gas field, proactively preparing for a carbon-neutral era.
American oil and gas company ExxonMobil has long promoted its CO₂ transport and injection technology for CO₂-EOR (CO₂-enhanced oil recovery) and has an MoU with Indonesia's Pertamina to build an offshore CCS hub. ExxonMobil also has plans to develop CCS projects with Petronas in Malaysia and is discussing depleted or high CO₂ gas fields near Sarawak for CO₂ storage. It recently announced plans for a Low-carbon Hydrogen Hub combining blue hydrogen and CCS.
Saudi-Aramco and Petrobras have announced CCS projects with CO₂-EOR with almost all energy companies having CCS projects underway or planned.
The International Energy Agency (IEA) reports that 35 commercial CCUS facilities are in operation worldwide, capturing 45 million tonnes of CO₂ per year, with more than 300 CCUS projects recently planned. Compared to active CO₂ capture projects, the IEA points to the lack of CO₂ transport and storage infrastructure as a problem. Only a fraction of the CO₂ captured can currently be transported, so investment in CO₂ transport and storage infrastructure is growing significantly to accommodate the increased volume. Meanwhile, LCO₂ carriers are also becoming increasingly important for the flexibility and long-distance transport of CCS projects. LCO₂ carriers are more efficient, can take CO₂ from a variety of capture sources, and have a shorter construction time compared to pipelines, especially for long-distance transport over 500 kilometers.
There are currently two 7,500-tonne CO₂ carriers under construction in China for the Northern Lights project and one 1,450-tonne CO₂ carrier under construction in Japan. LCO₂ carriers are linked to plans to build CO₂ hub terminals in major ports such as Antwerp in Belgium, Gdańsk in Poland, Gothenburg in Sweden and Dunkirk in France. CCUS projects are expected to become more active as a multi-user transport network of pipelines, hub terminals, and LCO₂ carriers is built, significantly increasing the demand for LCO₂ carriers. According to Clarksons' forecast, due to the nature of LCO₂ carriers ordered in connection with CCS projects, it makes difficult to specify the expected number of orders, carrying capacity and design. However, a large number of LCO₂ carrier orders are expected, mainly for long-term national projects.
South Korean companies are offering various blueprints for realizing a hydrogen economy. Hyundai Motor Company aims to supply 30,000 hydrogen vehicles and build 70 hydrogen refueling stations by 2030. However, due to the current limitations of green hydrogen production, it will have to rely on the production and supply of blue hydrogen after importing LNG and treating the produced CO₂ produced through CCS projects. To this end, Hyundai Engineering & Construction is developing CO₂ capture and liquefaction process technology and CO₂ hub terminal construction technology. SK E&S is building liquefied hydrogen plants in two cities in Korea, Incheon and Ulsan, which will produce blue hydrogen from LNG and treat the CO₂ through CCS projects. It plans to send 100,000 tonnes of CO₂ per year to the Santos Bayu-Undan CCS project and is planning to order four 40,000-tonne LCO₂ carriers.
Apart from the production of blue hydrogen, there are no alternative means of disposing of CO₂ from domestic power plants and steel mills. The Korean government, led by the Korea National Oil Corporation, is planning to re-use the Donghae-1 gas field as a CO₂ storage site. Currently, the planned storage capacity is 400,000 tonnes of CO₂ per year, which is far less than the country’s CO₂ emissions (656.2 million tonnes in 2020). In comparison, South Korea's Nationally Determined Contribution (NDC) target for 2030 is 10.3 Mt, with 4 Mt of CCS and 6.3 Mt of CCU planned. Until there is sufficient storage in the Western and Southern Sea aquifers, it is likely that domestically captured CO₂ will need to be transported to overseas storage sites. Orders for LCO₂ carriers will therefore be on the cards. CO-emitting countries with fewer CO₂ storage facilities, notably South Korea and Japan, have no choice but to send CO₂ to overseas storage facilities, so the capacity and design criteria of LCO₂ carriers are also of growing interest.
Securing LCO₂ carrier technology from a value chain perspective
There are currently no established design criteria for the exact storage capacity and range of LCO₂ carriers. The phase behavior of CO₂ differs significantly from that of crude oil, LNG and LPG, which are widely used in the shipping industry. Unlike LNG, LPG and crude oil, which can be transported under conditions such as high-pressure and low-temperature or high pressure and high temperature, LCO₂ must be transported under both high pressure and low temperature conditions. The triple point of pure CO₂ is -56.6℃ and 5.17 bar. To transport it as a dense liquid, the pressure must be greater than 5.17 bar and the temperature greater than -56.6℃ to avoid the formation of dry ice. While hydrocarbons remain liquid when stored cryogenically at 1 bar (LNG: - 162℃, LPG: - 42℃), CO₂ must be stored at temperatures and pressures above its triple point. A type C tank should therefore be considered. Various LCO₂ tank designs are currently proposed, with different LCO₂ storage requirements for short voyages of less than five days inshore and long voyages of more than five days offshore.
For short inshore voyages, tanks capable of withstanding pressure up to 20 bar, without a re-liquefaction system, are required. Long offshore voyages require tanks capable of withstanding pressure up to 7 bar with a re-liquefaction system. There has not been a great deal of research and development into large-capacity LCO₂ tanks to date. During loading and unloading, the temperature and pressure of the liquid CO₂ in the tank must be well controlled to avoid dry ice formation or evaporation. As the design of the storage tanks is not yet finalized, the boil-off rate is not fixed, and the CO₂ re-liquefaction systems are under development.
As LCO₂ carriers are closely linked to CCS projects, they are not limited to the issues of shipyards and shipowners but need to be addressed by industry partners from a CO₂ value chain perspective. Close collaboration between industry, academia and research institutes is more important than ever to ensure the technological competitiveness of the shipbuilding industry while meeting the demands of the carbon-neutral era.